第383号 ロールボックスパレット等を用いたユニットロード(2018年3月8日発行)
執筆者 | 久保田 精一 (合同会社サプライチェーン・ロジスティクス研究所 代表 / 城西大学経営学部 非常勤講師 / 運行管理者(貨物)) |
---|
執筆者略歴 ▼
目次
1.はじめに
生産性革命や働き方改革を推進するため物流業は目下変革を迫られているが、特に大きな課題はトラック輸送における長時間労働の改善である。
ドライバーの労働時間を短縮するうえでポイントとなるのは「運転・休息している以外のムダな時間」の削減であるが、その点で注目されている対策の一つが、荷役時間の短縮に繋がるユニットロード化の推進であり、国交省が掲げる「物流生産性革命」でもユニットロード化が推進されている。具体的には2016年度の補正予算からロールボックスパレット(カゴ車)等を用いた配送に利用される「テールゲートリフター」の導入費用の補助が導入されており、この12月に閣議決定された2017年度補正でも事業が継続する予定である(注1)。
注1: 平成29年度補正予算では2億円の助成が予定されているが、一件あたりの補助金額は削減される予定。
なお言うまでもなくユニットロード化の効果は時間短縮だけでない。物流現場作業において特に労働者への肉体的負荷が高いのはトラックからの積み卸しなどの荷役作業であり、ユニットロード化により積み替えの手間が削減されれば、労働環境の改善に繋がる。また、ドライバーは一般的に「荷扱い」のある輸送業務を避ける傾向があるが、ユニットロード化によって荷扱いが減れば、より多様な労働者の参画が可能となり、ドライバー不足の解消にも有効である。加えて、カゴ車を用いたユニットロードは、平パレットと異なり荷卸し先でフォークリフトが不要であることから、適用領域が広いことも利点となる。
一方で、カゴ車は平パレットと異なり、サイズの標準化が進んでいないなど様々な問題を抱えている。そこで本稿では、これらカゴ車(等)を用いたユニットロードシステムの現状を改めて整理し、当面の課題を考えてみたい。
(用語について)
以下では主として3面ないし4面を囲われた車輪付きの台車(図表1)をロールボックスパレットと呼ぶことする。なおロールボックスパレットの略称は「カゴ車」「カゴ台車」「カゴテナー」など様々であるが、ここでは「カゴ車」を用いる。また店舗内配送で利用される、両面から取り出せる6輪(または4輪)の台車(カートラックなどと呼ばれる)は本稿での議論には含めないこととする。
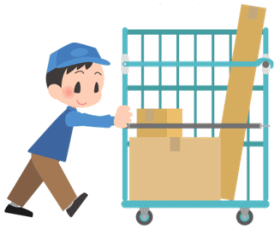
2.サイズ、規格等
1)サイズの不統一
カゴ車の外寸はJIS(日本工業規格、具体的にはJIS Z 0610)で規定されている。平面サイズはユニットロード寸法のISO規格とおおむね整合した規格となっており、具体的には「800×600」、「900×800」、「1100×1100」等が規定されている(いずれも外法寸法でmm単位)。例えば「800×600」はユーロパレット(1200×800)を二等分したサイズである。
一方で実際に販売されているものを見ると、下表のようなサイズが目立つ。表中黒丸を付した850ないし650サイズは主流サイズの一つだが、JIS規格外である。平パレットにおいてはJIS規格パレットが大半を占めるうえ特にT11サイズが広く普及しているのに対し、カゴ車においてはJIS規格サイズが相対的に少ないうえに、サイズがバラけている傾向がある。
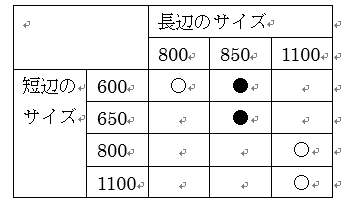
以上、平面寸法について述べたが、高さについてはJISでは「1800以下」との定めがあるのみである。
実際に販売されている製品を見ると、高さについては1700前後のものが大半で、ほかに1450サイズも比較的多く見られる。これよりも大きいサイズとしては、ボックスチャーターで利用されているカゴ車があり、有効内寸を1700取っている関係で車輪を含む外寸はより背高な規格となっている。
なお高さは安定性(転倒しやすさ)と密接に関係してくるが、JIS規格では、安定性に関する規定もある。具体的には無負荷のカゴ車が傾斜角20度の床面で転倒しないことを求めている。
20度の傾斜角は勾配では約37%に相当し、緩めの階段程度の非常にきつい坂道である(図表3)。よって通常の場面で利用する可能性は低いものの、ある研究機関の資料によると、「流通している大半のロールボックスパレットは、20度の傾きでは転倒してしまう」ため、「JIS規格に適合する製品はほとんど見られない」という(注2)。
以上のように見てくると、寸法等でISO規格との整合性が必要となる平パレットと比べると、カゴ車では規格と実態との乖離が大きいことが分かる。
注2: 独立行政法人 労働安全衛生総合研究所「ロールボックスパレット起因災害防止に関する手引き」2015
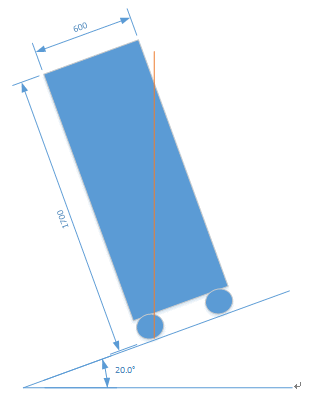
2)積載効率の低下
前項で見たようにサイズが不統一であると、複数のカゴ車を積み合わせる場合に積載効率が低下することは言うまでもない。これに加えて、高さ方向の有効利用が困難であることも問題である。
カゴ車は安定性を高めるために車輪の外径を大きめに取らざるを得ないこと等から、有効内寸が低下せざるを得ず、外寸1700のカゴ車でも有効内寸は1450程度に留まる。これは15%程度のデッドスペースに相当する。
また、集配送で利用される中型車の荷台の有効高さは2100程度、幹線輸送で利用される大型車の場合は2400程度だが、高さ外寸1700のカゴ車では、上方にかなりのデッドスペースが生じてしまう。
包装容器とカゴ車の平面内寸の不整合による積載効率の低下は、設計の見直しによってある程度改善可能だと思われるが、トータルでの積載効率の低下は無視できないレベルである。直積みする場合と比較した場合のトータルでの積載効率の低下は50%近くに及ぶ場合もあり、適用領域が限定される原因となっている。
3.レンタルの仕組みと回収輸送
平パレットと比べて見た大きな課題は、「パレットプール」に相当する社会全体で資産を共有する仕組みが未整備であることである。パレットプールのような仕組みがないと、カゴ車を回収するために車両を仕立てて輸送する必要が生じ、コストや環境負荷も増大する。
現状を見ると、カゴ車は卸の流通センターから店舗までといった、比較的狭い範囲で閉じた運用をされる場合が多いことから大きな問題となっていないが、広域でのユニットロード運用を行うには回収輸送がネックとなる。
なおカゴ車でパレットプールのような仕組みが普及しない理由は、平パレットとのサプライチェーン上の費用負担構造の違いがある。
平パレットは、メーカーが自社の負担によって、製品の買い手である卸・小売にパレットを貸し出す仕組みがベースにある。その際、卸・小売がパレットを紛失してもメーカーから費用負担を求めるのは難しいため、パレットプールを利用する意義が大きい。これに対してカゴ車は、小売業等が自社専用品をベンダーに貸与して利用させるケースが多く、紛失時の責任追及が容易である。
このような違いがあるとはいえ、全体最適の観点から言えば、社会全体で資産をプールする仕組みを構築する方が、経済的観点からも環境負荷の観点からも望ましいはずである。
4.安全性
前掲資料(注2)によると、カゴ車に起因する労働災害は全体の0.83 %(平成18年、サンプル調査)であり、年間では千件超の事故が起きていると推計されている。これはカゴ車という輸送器具に限定した件数としては明らかに多く、安全性の確保に課題があることが伺える(ただし、カゴ車を利用することで、腰痛等の労災が予防されるプラスの効果もあることも留意すべきである)。
1)法令上の位置づけ
荷役に用いる機械器具(フォークリフト等)については労働安全衛生法で諸々の規定があるが、パレット全般について若干の規定がある以外(例えば労働安全衛生規則第151条19)、カゴ車に関する規定は見あたらない。
次に店舗への納品など、カゴ車が道路上を通行するケースは少なくないことから、道路交通法における規定を見てみると、道交法では、「荷車その他人若しくは動物の力により…牽引され」る車両は軽車両と規定されている。自転車などと同様に軽車両は、保安基準(道路運送車両の保安基準)が適用されるが、カゴ車は「乗用の軽車両」ではないため、目立った規定はない。例えば制動装置(ブレーキ)を装備する義務もない(保安基準第70条)。
なお保安基準自体には積載重量に関する規定はないが、道交法では都道府県公安委員会が軽車両の積載重量を定めることを認めている(道交法第57条)。これを受けて例えば東京都では、「牛馬車及び大車以外の荷車にあっては450キログラムをこえないこと」と積載重量の規定を設けている(東京都道路交通規則第10条、なお大車とは荷台が1.65㎡以上の荷車である)。
軽トラックの積載重量が350kgであることから考えて、450kgという制限はかなり余裕を持たせて設定したものと思われるが、カゴ車の場合600kg程度まで積載されるのが実態であり、規定の有効性にやや疑問が残るところである。
このように法制度上は特記すべき規定は見あたらないが、JISの法的拘束力は限られることから、最低限の安全を確保するための基準もないのが実態である。
2)積載重量と安全設備との関連
道路上で利用するケースを除外したとしても、カゴ車の積載重量の大きさは様々な問題を派生させる。ブレーキの装備は多くのカゴ車が備えているが、ごく簡素なものがほとんどである。JIS規格の20度は論外としても、より緩やかなスロープでもブレーキが効かないことがある。構内や路上でカゴ車が勢いを付けて滑走を始めた場合に、これを人手で制止するのは難しい。
また、フルに積載したカゴ車は、緩やかなスロープ上でも移動させるのは物理的に困難である。例えば英国の安全衛生庁(HSE)の報告書では、傾斜角約3度(約5%勾配)のスロープを女性が移動させる限界重量として256kgという数値を挙げているが(注3)、トラックからの出し入れ、路側の段差、店舗入り口の段差など、5%程度の勾配を走行するケースは一般的であると考えられ、積載重量を制限しない限り荷役作業を安全に行うことは難しい。
カゴ車は、このほかにも満載した場合の見通しの悪さなど様々な課題が指摘されるが、最大の問題はやはり積載重量である。
注3: Safety of roll containers, the Health and Safety Laboratory for the Health and Safety Executive, UK, 2002
なお規格がEUと日本とは異なるため、あくまで参考として挙げる。
3)安全マニュアルの策定と課題
以上で述べたようなカゴ車の安全性を巡る問題点については国においても認識が高まっており、上記の手引き(注2)のほか、「ロールボックスパレット使用時の労働災害防止マニュアル」(厚労省、(独)労働安全衛生総合研究所)、「陸上貨物運送事業における荷役作業の安全対策ガイドライン」(厚労省、陸上貨物運送事業労働災害防止協会)などの資料が作成・公表されている。特に前者の「マニュアル」は簡潔にポイントが整理されており、現場管理者には必読の内容である(注4)。
マニュアルで挙げられているポイントは下記の8点であり、いずれも抑えておくべき基本動作である。
注4: 次からダウンロードできる。(クリック時、別ウィンドウでオープン)
http://www.mhlw.go.jp/stf/seisakunitsuite/bunya/0000098500.html
なお、マニュアルの内容は路線便等の大量の貨物を扱う現場には適合する一方、卸・小売等の物流センターの実態とは乖離しているのも事実である。例えば店舗のバックヤードから店頭への横持ちの場面で、マニュアルに書かれた対策を取ることは難しいだろう。とはいえ、現場管理者としては、マニュアル全体でなくとも、自社で利用可能なポイントだけでも参考として活用することが望ましい。
5.自動化や機械化との親和性
カゴ車をユニットロードとして荷扱いする場合には、工程間横持ち、保管場所への移動等は手作業で行う場合が大半である。しかしながら、生産性向上の観点からは、これら単純な繰り返し作業は自動化・機械化したいところである。
カゴ車に対する自動化・機械化には様々な方式が見られるが、古くから見られるパターンの一つは、ロールボックスパレットに牽引棒(トウバー)を設置し、複数を連結してターレのような搬送車で移動するパターンである。このパターンは国内では花き市場などで見ることができる。また、床下や床上に設置したコンベアでカゴ車を引っかけて、搬送する例も多く見られる。このほか、近年はAGV(無人搬送車)で搬送する例も出てきており、例えばヤマトの関西GWではクール便のロールボックスパレットをAGVが搬送しているという。
このほか、下図に挙げるように多種多様な方式が考案されているが、それぞれ独自の牽引機構をカゴ車に設置するなど汎用性に欠けている点が課題である。
平パレットはそもそも、フォークリフトや自動倉庫での利用を想定した設計となっているのに対し、カゴ車は設計や規格の段階で機械化が想定されていない。そのため今後普及が見込まれる、AGVや自動搬送ロボット(図表6)との連携方法を改めて検討する必要があろう。
- http://www.egemin-automation.com/en/automation/material-handling-automation_ha-solutions_in-floor-chain-conveyors_etow-concept-solutions/roll-container-transport
- http://conveyorsystems.nl/elevator-for-pallets-and-containers/
- https://www.logismarket.es/sumal/roll-container-chapa-lector-agv/4592067914-9532759-p.html
以上
(C)2018 Seiichi Kubota & Sakata Warehouse, Inc.