Service for Electronics Industries(electrical machinery,industrial machinery, medical equipment)
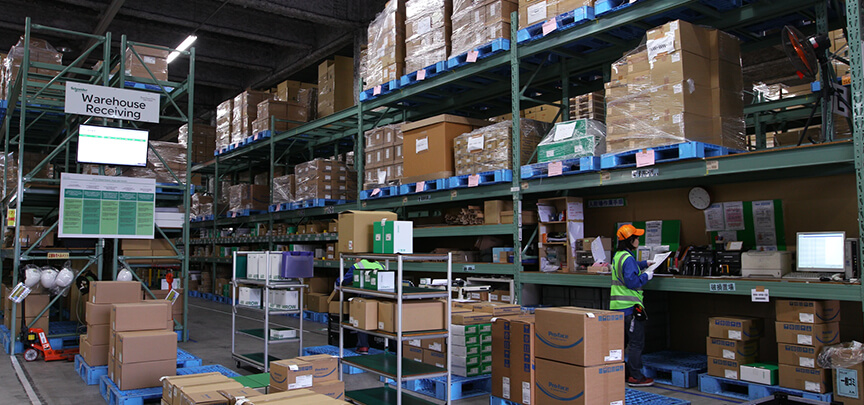
we provide our customers with high-precision logistics quality and services.
Sakata Warehouse has developed various know-hows through implementation of logistics businesses for Electrical Machinery Industry over 20 years.
We confidently provide our customers with high-precision logistics services such as picking and assembly processing of tens of thousands of parts by lot number, operation and process management of logistics operations, transportation and delivery management, and construction of logistics information systems that realize labor saving and high quality.
Also, our staff – specialists of electronics logistics business – support clients for their logistics innovation as the stance of their agent. We also provide operation outsourcing services to the clients using their assets effectively.
Warehouse/3PL service video for Electronics Industries
MOVIE
(Service for Electronics Industries)
Sakata Warehouse has cultivated various know-how through the implementation of logistics operations in the electronics industries for over 20 years.
Introducing the electrical parts distribution and 3PL service (movie) at the Izumiotsu Sales Office, which is a distribution center that supports manufacturing services such as BTO, inspection and repair.
Distribution in the electronics industry (electrical components, industrial machinery components, and medical equipment)
The Structure of the Electrical machinery + Industrial machinery and Medical equipment industries
The following is a diagrammatic representation of the distribution channels in the electronics, industrial machinery, and medical equipment industries.
In some cases, the distribution of assembled parts goes through wholesalers or trading companies to the users, but in most cases, the parts are sent directly to the factory or the delivery site in the factory with the delivery destination’s specific “actual goods slip” / “shipping instructions” attached.
It is also necessary to create BTO or set products and handle inspection/repair work according to customer requirements.
Value/strength


The followings are listed the problems and the request matters in the electrical machinery and industrial equipment industry summarized originally by our company.
1-1.The problems about a physical distribution (example)
- Neither product number nor a brand name is displayed on your goods, and the goods required to manage assembly processing and ship with machinery attachment also exist; therefore you depend on a experienced son of charge in affairs about shipment. From such a situation, you would like to manage on a system to prevent shipping error may be exerted on a customer’s production.
- It’s required the exclusive shipping service for the exact correspondence to each designation of delivery date. But you must correspond to customer’s demands that shipment cancellation required by client and the urgent shipping that a shortage of parts arrived. So the method of delivery date management is complicated
- There is demanded strict rules for cargo in method of packing and attachment of the designation of the statement; You need an experienced son of charge in affairs who can observe a regular procedure to prevent objection. As result, the operating cost has increased.
- It’s needed a experienced son of charge in affairs to manage assembly processing, tests on the working of a machine and repairing based on the client’s requirement.
- Shipping record management by the Serial No. unit as well as lot No. management are sometimes required. In order to take extreme measures with the survey, the survey may not be able to correspond accurately.
- As Just in time delivery becomes popular, it is necessary to shorten lead time for business. Shortening lead time requires extra expenses, which gives you a headache as it influences price competitiveness. Urgent delivery upon customer’s request is necessary to be arranged.as well.
- Agents’ requests high quality of logistics, and if you make miss delivery or shipment damages, porters or messenger bikes must be chartered at your own cost for completing delivery. To maintain business, such mistakes and damage in the shipment must be avoided.
1-2.Requirements from the owner of goods (examples)
- Respond to individual requests from customers (delivery destinations), further improve logistics quality, and promote standardization through logistics information systemization to prevent erroneous shipments.
- They would like to arrange and systematize about the correspondence to the individual request from the customer and to structure the same quality service to the customer.
- They want to improve logistics quality comprehensively by arrange and formalization about goods which are easy to mistake and control item for irregular.
- They want to build the structure that goods without a bar code and product number can also manage by bar code
- They want to correspond to BTO (place the stock as a component form and build the product in response to the customer’s order and ship), set parts (to combine different parts) and repair products to improve service quality and sales expansion.
- To make it easy to get shipping record information by the key word such as destination name, date of shipment, lot No., serial No., order No., or shipment No. In addition, I also want to simplify search of past delivery notes and trucker’s bills.
- Combined with various distributors, I want to adopt a balance between shipping costs and delivery lead time.
- In order not to generate unnecessary shipping costs, I want to eliminate miss delivery shipment and product damage.

Sakata warehouse’s 3PL service will
solve these problems!

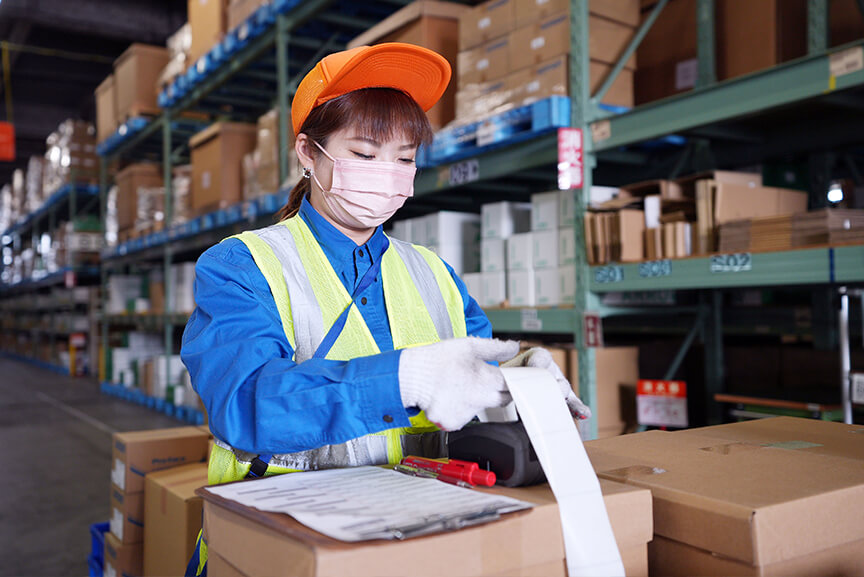
1.Individual-based management by “the stock label” at the arrival
As many you can see that in many cases they have no number tag or no name tag on each parts. So we issue and attach “the stock label” at the arrival, and provide individual-based management using bar code. Also, exact inventory control and inspection using bar code upon shipping are possible by performing location management by a goods lot unit at the time of goods storing. We has developed various know-hows through implementation of logistics businesses for industrial machinery bushiness over many years. Therefore, we provide our customers our high precision logistics services.
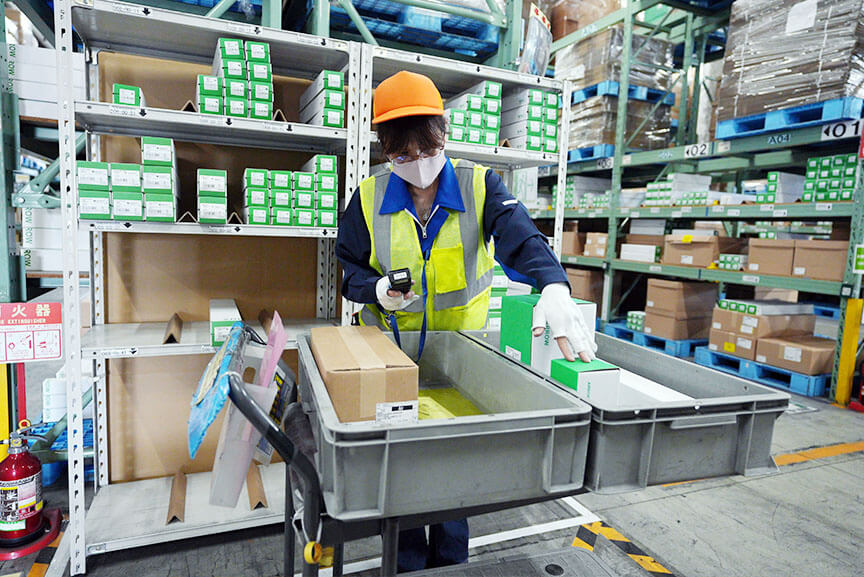
2.The shipping record management by each serial No. is realized on both operation and system.
By implementing of our own management system, it is possible to simplify the shipping record management of lot no. and serial no. which are terribly complicated by paper based filing. Also for its operation, it is possible to make a proposal of the best operation scheme for the production identity and matching the shipping and receiving by serial no.
Taking advantage of our expertise which has been created by many years of experience in the electronic components industry, we improve the operation efficiency building a storage and working space layout according to the frequency of shipping by each product.
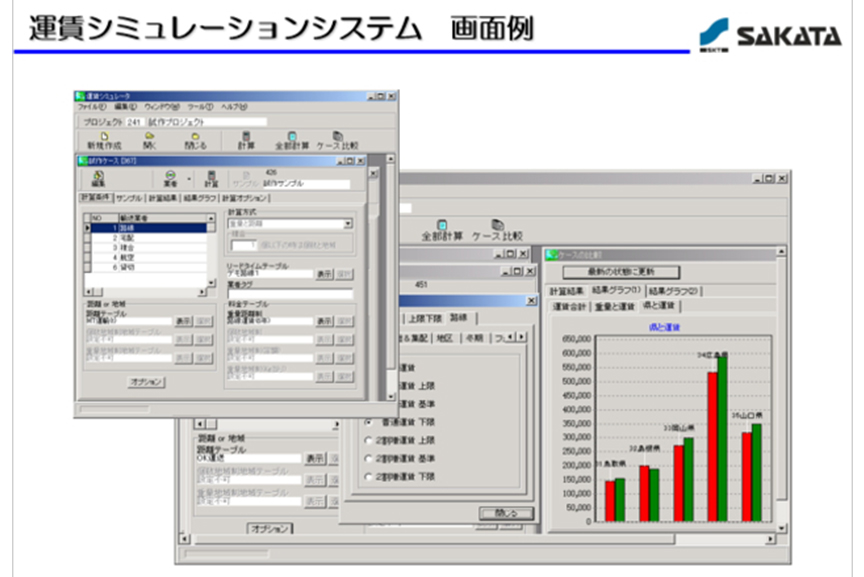
3.Optimizing by combining shipping companies
Based on past shipping performances, we divide shipping operations to several contracted shipping companies by destination area, shipping volume lot, delivery conditions such as time appointed service. With highly accurate simulation and data entry of delivery record / shipping lead time into our system, we can provide better quality and accurate shipping management and cost reduction.
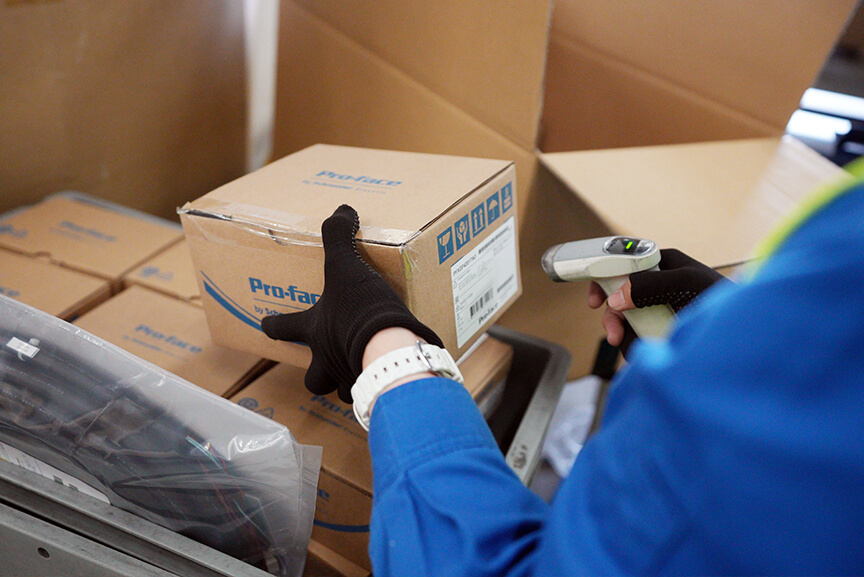
4.Building systems and implement them to reduce shipping errors
Based on dimension data in production master, we can realize our own packaging calculation systematically. By clarifying every package (every tag), as we can make a picking and an inspection by the list of each packing, operators will have no trouble of selecting boxes and the rest of odd items.
Also in addition to operation standardization, by introducing the inspection system that connects labels and picking lists with bar cord handy terminals, we can help improving of shipping accuracy by package units.
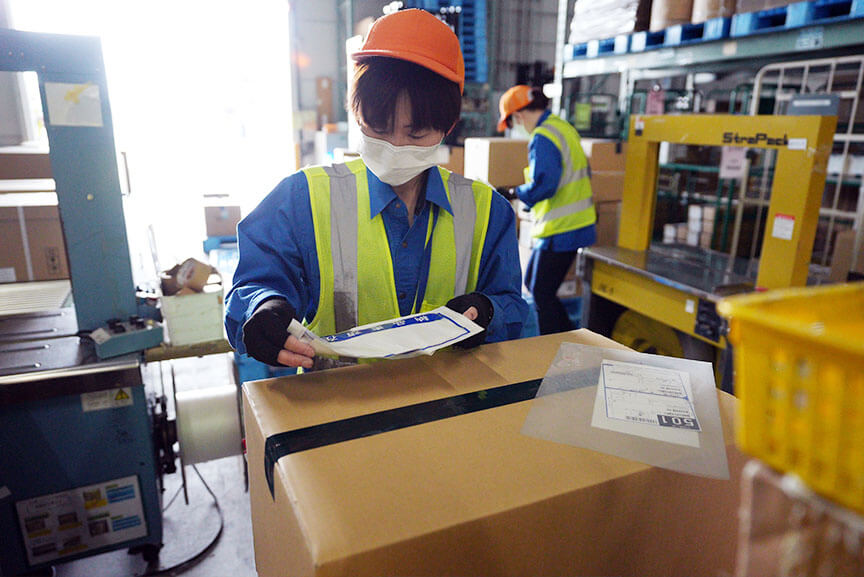
5.Optimizing by combining shipping companies and delivery date control
Based on the data for the shipping instruction, our WMS/TMS selects the best shipping company of various shipping companies by calculating lead time(LT) and delivery date control. Also, the urgent shipping that a shortage of parts arrived is available on the day.
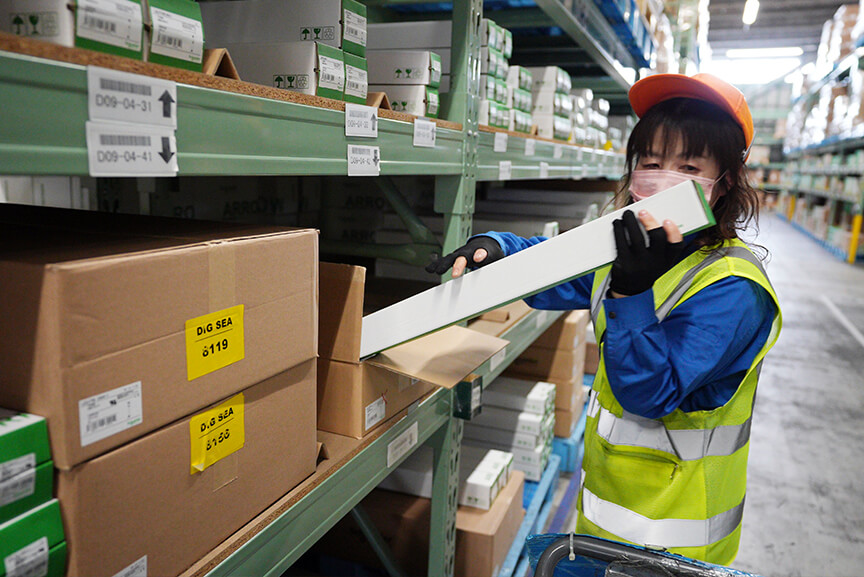
6.Management to prevent shipping error and compile system
By resistering a picture into the inventory data of irregular goods such as set parts (to combine different parts) with accessories, anyone can distinguish goods by the picture in the case of inspection by POS inspection system or packing.
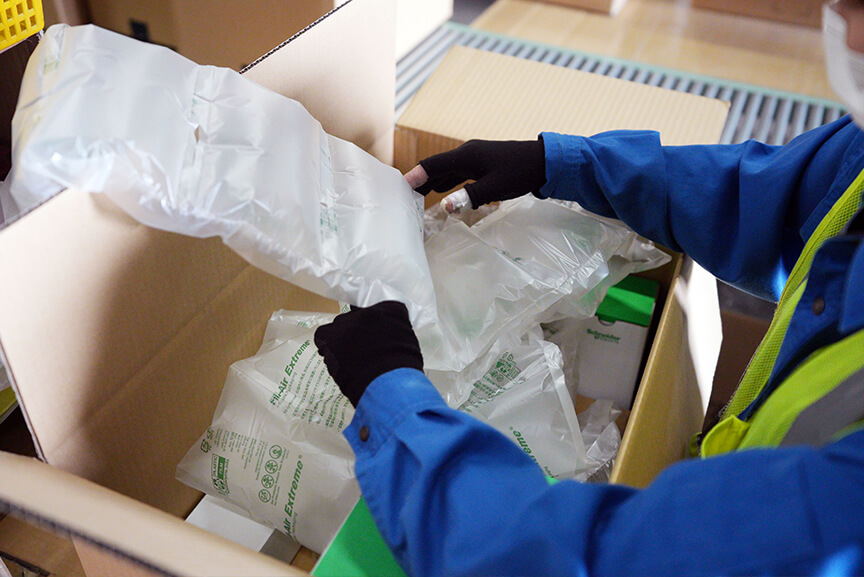
7.Individual-based management in response to the customer’s order (packing form, way to issue/ attach “the identification tag” and “the shipping instruction”)
For popular to industrial machinery business based on each delivery of goods place, it’s possible to manage packing form, issue of the identification tag, and the attachment method in a unified manner on a system. Therefore Mieruka(Visualization) and standardization of work are realized by displaying it on a POS inspection system screen.
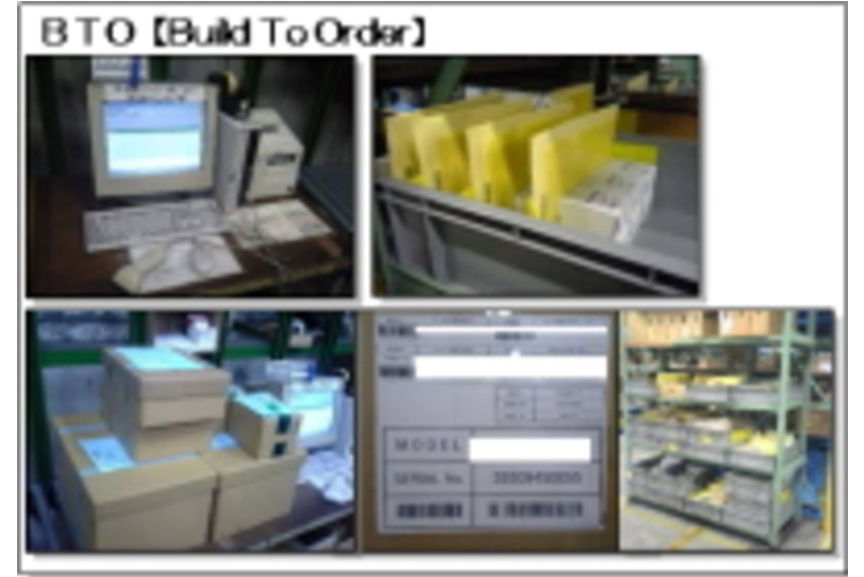
8.Support for BTO, set product creation, “repair center” and “customer support center” operation
We can handle the creation of BTO and set products at the request of delivery partners, and implement processing operations and progress management.
In addition, we can operate a repair center to repair defective products after receiving and inspecting them, as well as a customer support center to respond to inquiries from customers regarding product information and repairs.
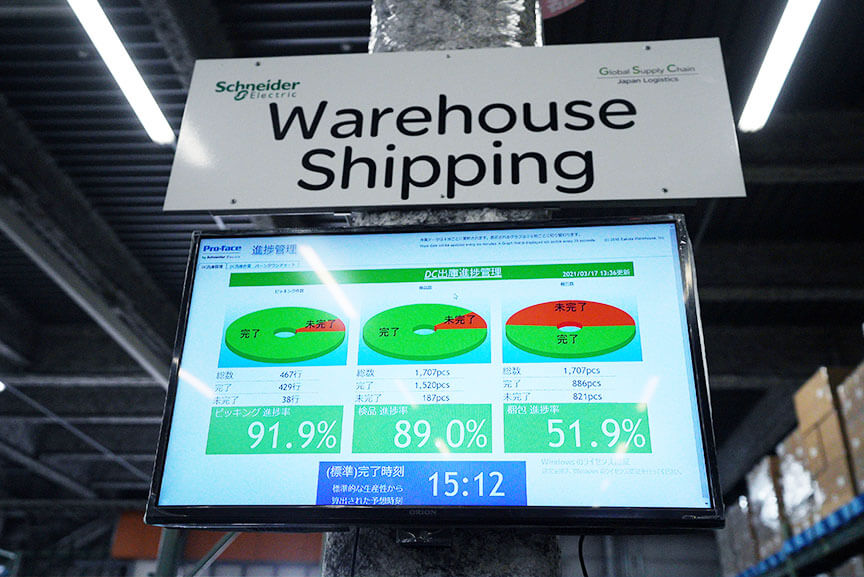
9.Responding smoothly to client/sales inquiries by managing shipping status
By working with shipping companies, we realize MIERUKA (visualizing) of shipping from warehouse to the delivery destination by our system which can create unique shipping numbers matching with customers order number / invoice number, by managing systematically order numbers, shipping numbers, and shipping charges through our system.

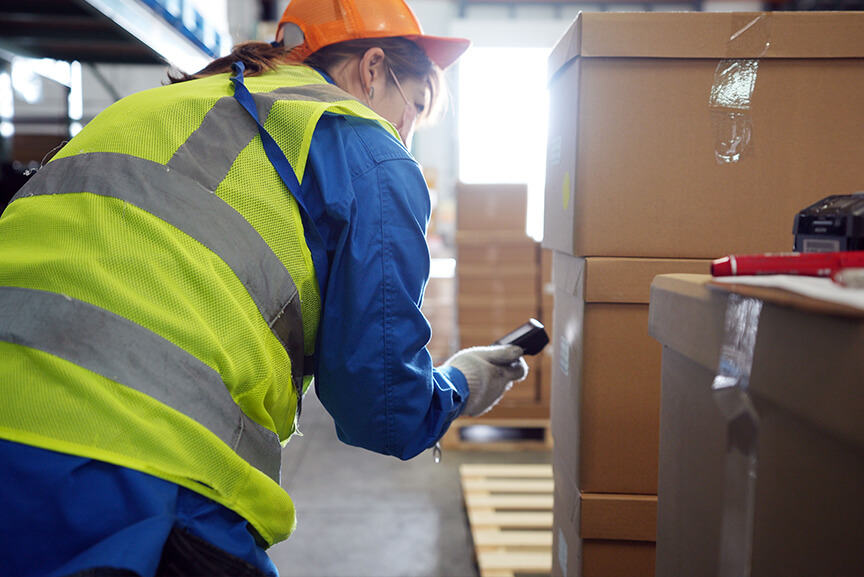
1.Improving individual product control and inventory management accuracy
Previously, unless we count products at the location of each storage location, the existence of exact stock quantities and goods was not able to be recognized. Updating of inventory data in real time and the storing system for goods without the character of the product code and the brand name by The arrival-of-goods label corresponding to a bar code and HT make the link between the location code and inventory data correctly.As a result, inventory accuracy was sharply raised. Moreover, by the system which can search history of storage and retrieval for every lot code, a cause when inferior goods are found, and the whereabouts of the responsibility range were able to be clarified.
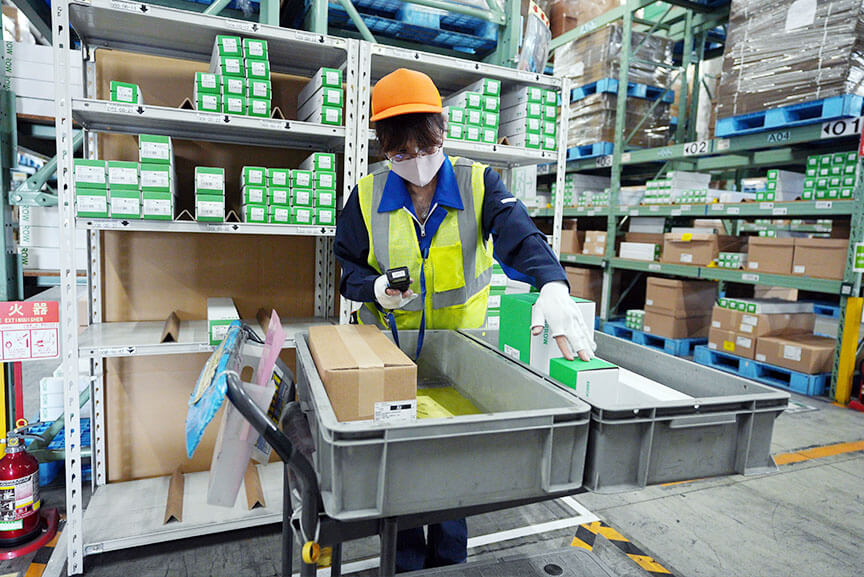
2.Improvement of tracing products accuracy and clarifying responsible party for each operation
Before its implementation, it has taken burdensome works like tracing back serial numbers or invoice copies to clarify. However, our new system supports history searching and its implementation causes to dramatically reduce your work.
When any problems arose, because of that it became possible to trace a product in detail such as in which production line it came from and to in what order it had been produced, we could now clarify the cause of the problem and find out where the responsibility lay.
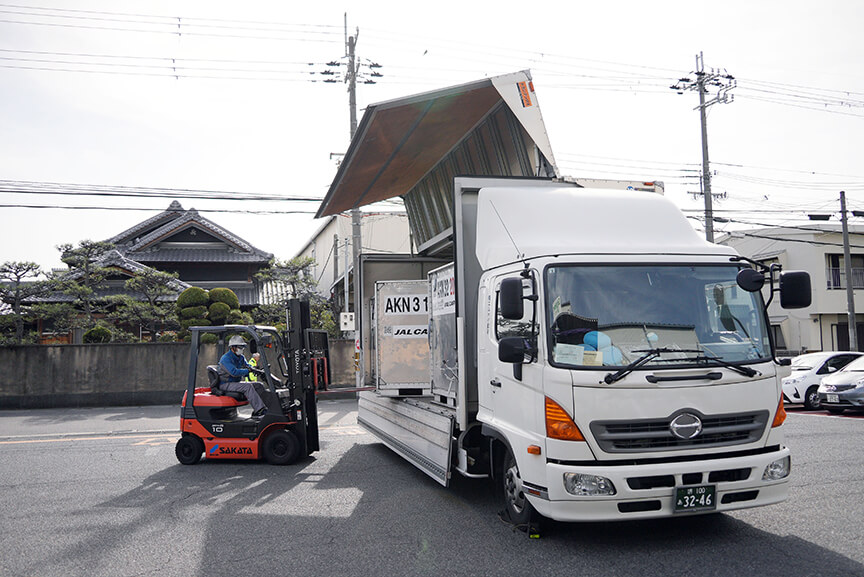
3.Reducing shipping costs and establishing short lead times
After outsourcing, we combine different courier companies effectively though those carrier companies couldn’t make it before outsourcing. So we can balance shipping fees and lead times, satisfying customers.
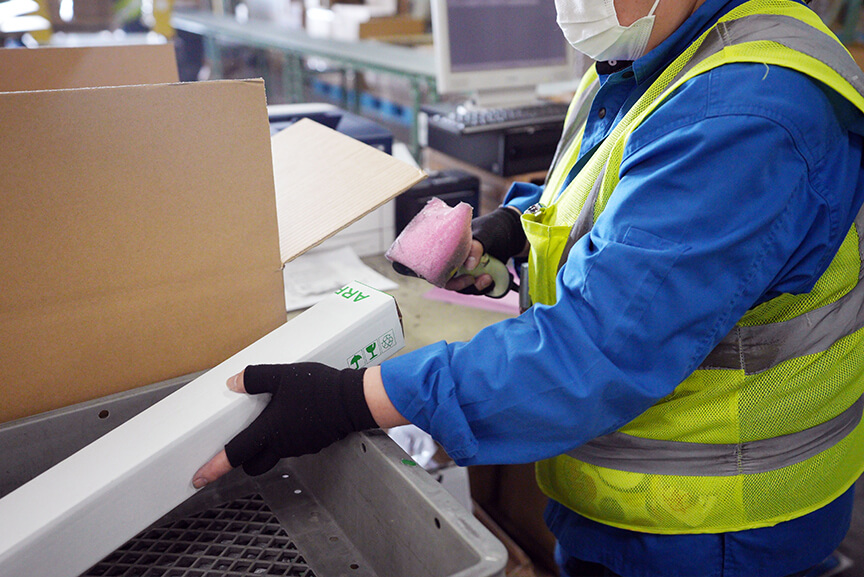
4.Reducing shipping errors
Before we relied on operators’ experiences, but we switched to easy operations anyone can remember, so anyone can be like an expert after getting used to it a bit. As a result, we have been able to reduce overall shipping errors.
Human errors are greatly decreased by excluding visually inspect, and adopting inspect by reading bar codes with handy terminal.
(We achieved less than one-hundred thousandth error rate.) Also, it enabled to detect error in bar code display in its early stage and suspend doubtful products in warehouse.
As a result, it decreased inconveniencing customers.
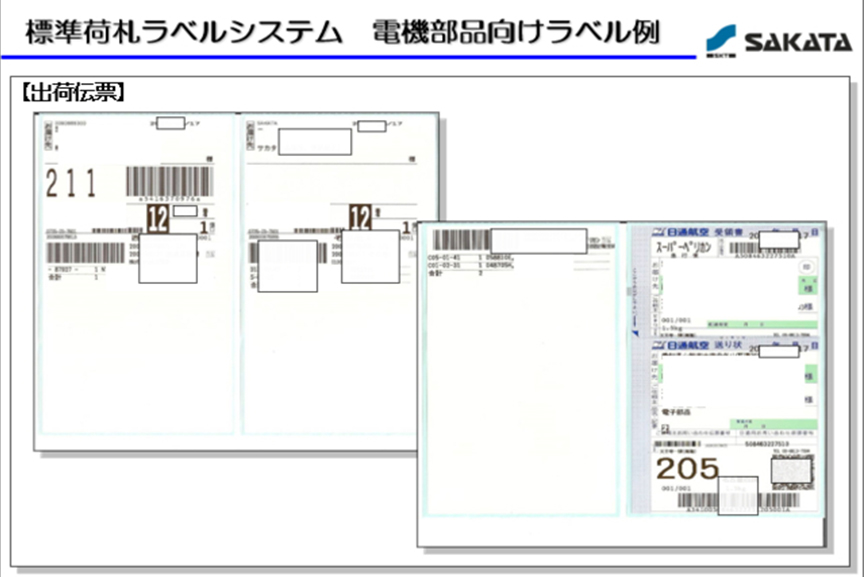
5.Observance of a designated delivery day, and improvement in transportation and delivery quality
According to link with TMS and “the standard label system”*1 by EDI with shipping companies, we can select the optimal shipping company for the combination of shipping charge and lead time. Thus, since we provide services such as observance of a designated delivery day, management of shipping companies designated by the customer and improvement in transportation and delivery quality improvement in the customer satisfaction was realized.
Note:*1. “The standard label system” is ourown system which issues a label combined “the transportation tag” function for several shipping companies with “the shipping label” function for our DC.
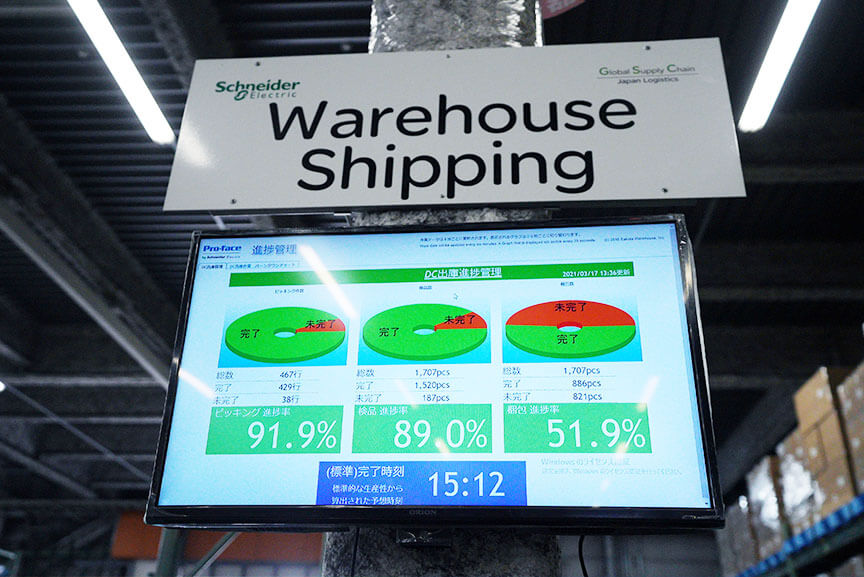
6.Improvement in Total Logistics Quality by MIERUKA(visualizing)
By using the system of MIERUKA(visualizing) at arrival and shipping, the progress of work and the existence of stockout of parts for every order number can be checked immediately. As a result, routine work increased the efficiency. Moreover, this system is helpful in improvement of customer’s reliability in terms of management of irregular treatments for shipment cancellation and urgent shipment. So we can improve in total logistics quality.
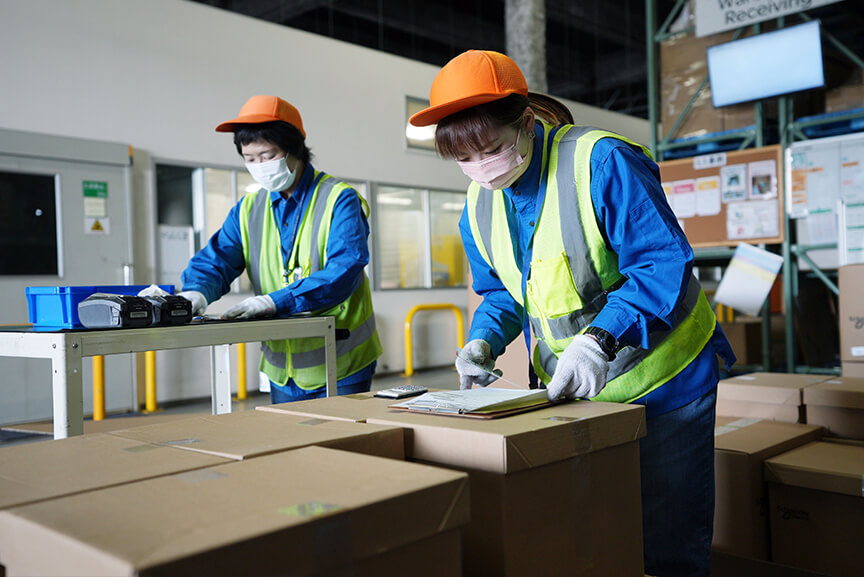
7.Standardization of operations and reducing shipping errors and objections from customers
By using barcodes and HT, we have not only improved the accuracy of each process of receiving, storing, and shipping, but we have also systematized and registered the individual requests of each customer and special products
(EX. attached accessories, set products, etc.), which used to rely on the experience of workers, and managed them in the system.
So we can maintain our logistics service quality at the time of staffs aid of a peak season too, and decrease objections from customers.
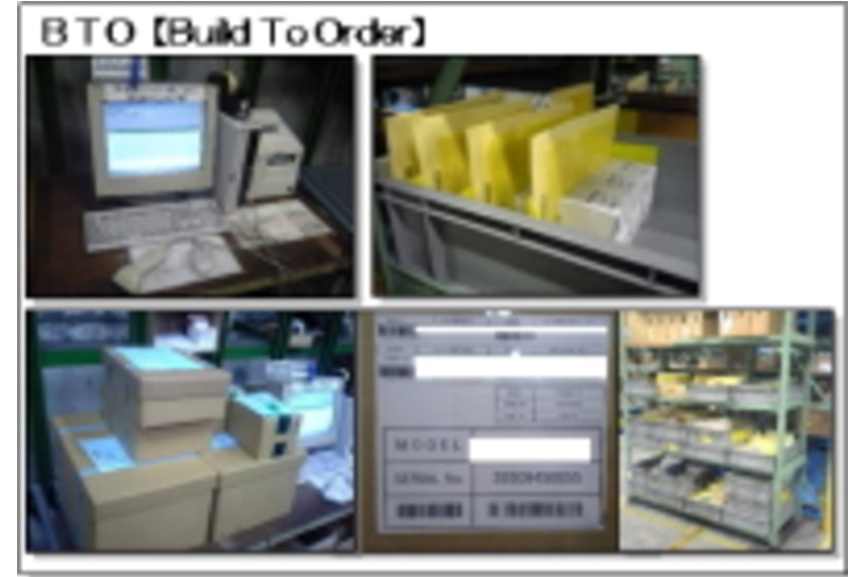
8.Improvement in customer service by promoting “Mieruka”(visualization) of set parts (to combine different parts) and BTO(Build to Order), and founding “the repair center”, and “the customer support center”.
Systematization of progress management of BTO and set parts (to combine different parts) realized improvement in customer service such as optimization of the inventory control of parts, or missing item management and the prompt reply of the time of delivery. Also, we realize improvement in customer service by promoting “standardization efforts” and “MIERUKA”(visualization) by product database system based on product database system of “the repair center” and “the customer support center”. *2
Note: *2.About repair products, it’s presuppose that we need you to receive the engineer’s guidance of your company throughout a fixed term and acquire skills. It’s available to response inquiry about products of skill information on condition that it registers to a database in advance.

9.Speeding up the response to inquiry
The MIERUKA (visualization) of delivery status could make a steeply improvement of response to inquiry from our customers. Also, achieved quick response made us more trustworthy.
Service Q&A

The following is a list of frequently asked questions and answers about our 3PL service in the electrical machinery and industrial equipment industry.
Improvements in logistics consulting analysis by (paid), posing challenges, from suggestions for improvement, Sakata warehouse is developing a one stop service until ( 3PL warehousing services) of actual business practice. Improvements in logistics, distribution system reconstruction, such as cost control (reduction), but about logistics, please feel free to contact us.
Responding to imported parts/barcode inspection, merchandise verification based on ASN (pre-arrival information), and inventory label issue/attachment, we report actual data on receiving inspection. Also, by appearance inspection and simple continuity tests (customers have to train), we can separate good parts and defective parts and process orders only for good parts based on actual data reports.
With our firm’s WMS/warehouse 3PL service, we can handle domestic distribution center operations including product shipping status, product inspection status, and operation status inside the distribution center, and shipping status and link data with the client’s ERP system as status information.
In the part industry, based on the client’s requirements, you need to combine different parts and deliver them just in time. Based on the client’s processing plans and priorities, we prepare and separate necessary parts and manage machining operation status, part security, and transfers by using the barcode control system based on the client’s order numbers.
We can provide management of delivery lot number per delivery destination and also serial number achievement control *1 of delivered products. You can also trust us to carry out bundling and inventory control for accessories (manuals, CD-ROM etc.)of a product or product sets.
Note *1. In order to carry out serial number delivery achievement control, serial number barcode for each product needs to be displayed in advance.
Our TMS enables managing lead time for delivery by several delivery companies using the system and enables system management of delivery date by back-calculating the specified delivery date that has been registered in our system in advance. Also, aside from the place of checkup, we carry out registry management of direct shipment address for each factory building and issue and attach JEITA(EIAJ) delivery slip to shipping boxes. Regarding dedicated slips for specified factories and particular delivery form through dedicated operation, these can be provided *2 as options.
Note: * 2. Separately, support the delivery of individual service, additional charge is required and shipping costs.
We not only repair and tests on the working of a machine in “the repairing center” but also response inquiry and consultation about products and repair in the customer support center. *3 We arrange and systematize customer needs and manage them.
Note: * 3. About repair products, it’s presuppose that we need you to receive the engineer‘s guidance of your company throughout a fixed term and acquire skills. It’s available to response inquiry about products of skill information on condition that it registers to a database in advance.
3PL service list

SAKATA WAREHOUSE will propose and support the realization of consistent “Supply Chain Logistics” from your domestic suppliers to end users.
We would like to introduce our 3PL service for the electrical machinery + industrial machinery, medical equipment industry.
Overall picture of logistics outsourcing
(1)3PL Services
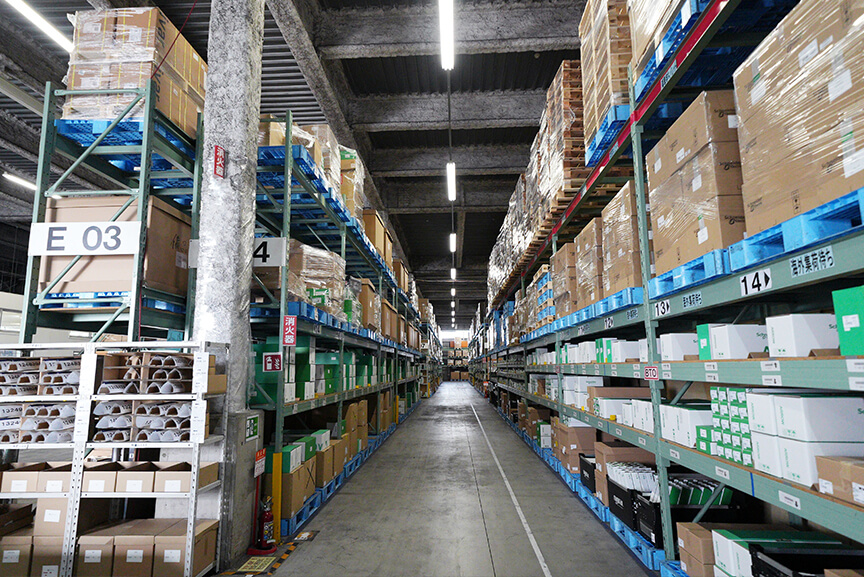
1.Inventory control(storage)
Using WMS (Warehouse Management System), a system developed originally by Sakata Group which has many actual operative performances in electrical products and parts logistics business, we manage our inventory. It interacts with inventory input and output and also with location management, and it enables the actual and real-time stock counting in SKU (piece), as well as physical management of sets, individual products with attached parts, and maintenance parts.

2.Transportation and Delivery
Using our simulation systems, we will select and combine the most suited transportation and delivery method (mode of transportation, companies) to our customers. By tracking information of goods and completion of delivery information by EDI with several delivery companies, we will quickly respond to the destination party (factory, agent and etc.) inquiries about the delivery status.
Also we will promptly provide our customers with shipping information and delivery completion information by E-mail. We also provide the customers the status of international transportation, Customs clearance and domestic delivery including procurement and trading operations for international forwarding by various alliance companies partnership.
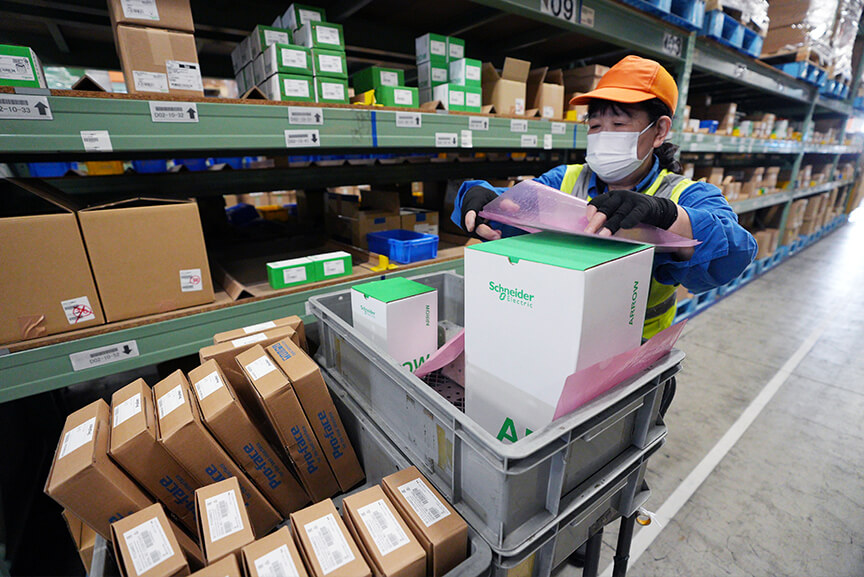
3.Piece picking
We will correspond to piece picking not only for product lot management but also shipping record management per serial number, piece picking for the presence or absence of set items/accessory parts, and bundled shipping of the product attached instruction (product manual etc.).
We also provide shipping on specified delivery date by just-in-time and follow defined procedure manual for shipment of products in emergency situations.
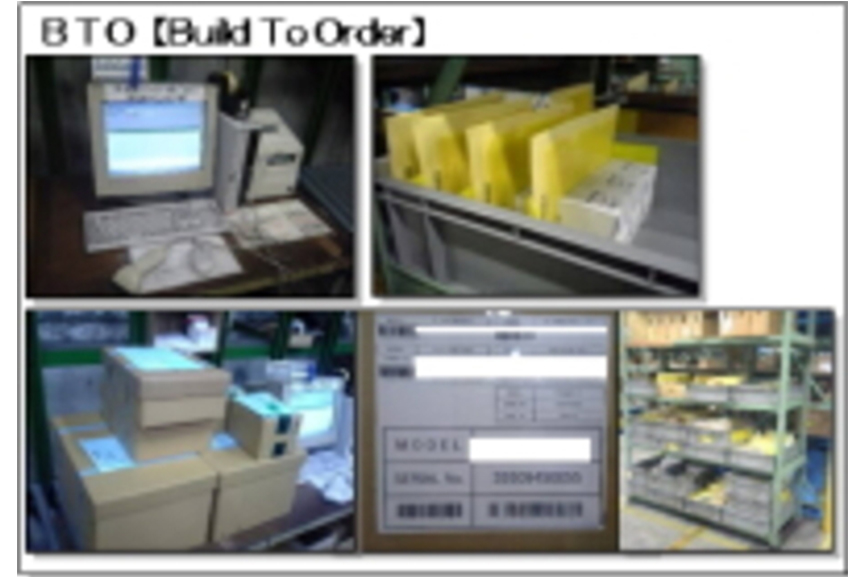
4.BTO (Bill to Order)
We will respond to BTO (place the stock as a component form and build the product in response to the customer’s order and ship) and set products, inspecting and repairing products and parts, managing the progress of processing work, and status management of finished goods, managing as representative product number of various products and picking of each product required for processing.
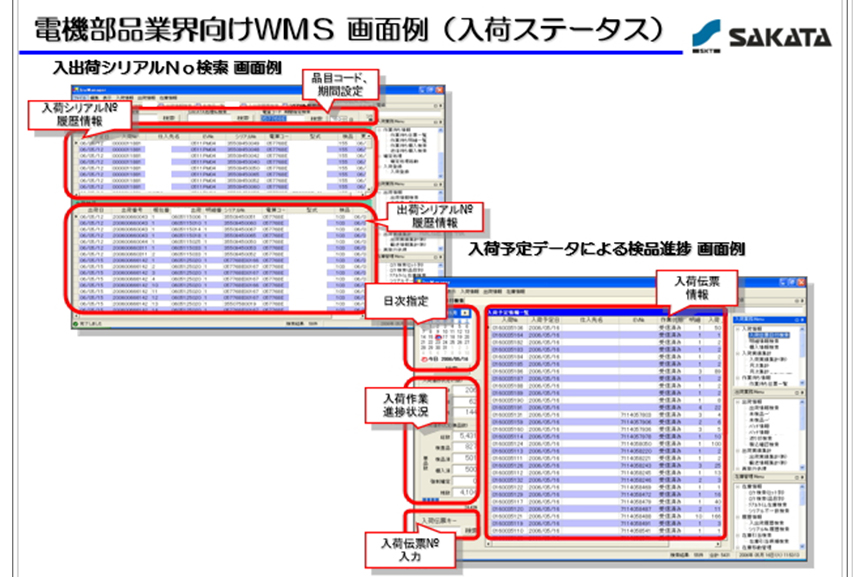
5.Information System
In addition to the Warehouse Management System (WMS) proven, we can provide total operation management by our Total Logistics Management System covering whole customer’s Supply Chain from “order processing” to “delivery products to the end users”.
This Total Logistics Management System includes the following systems.
A receiving inspection system based on advance shipping schedule data (ASN)
A system for issuing delivery destination-specific “present goods sheets” and “shipping instructions” linked to the piece picking system
A system for issuing cargo tag labels.
POS inspection system for inspection and packing
POS inspection system at the time of inspection and packing, – Warning system with image display and voice for irregular contents at the time of inspection and packing
(e.g.) Packing method specific to the delivery destination, method of attaching the “goods list” or “shipping instructions,” or presence of set items or accessories, etc.
Transport and delivery management systems, export packaging systems, etc.
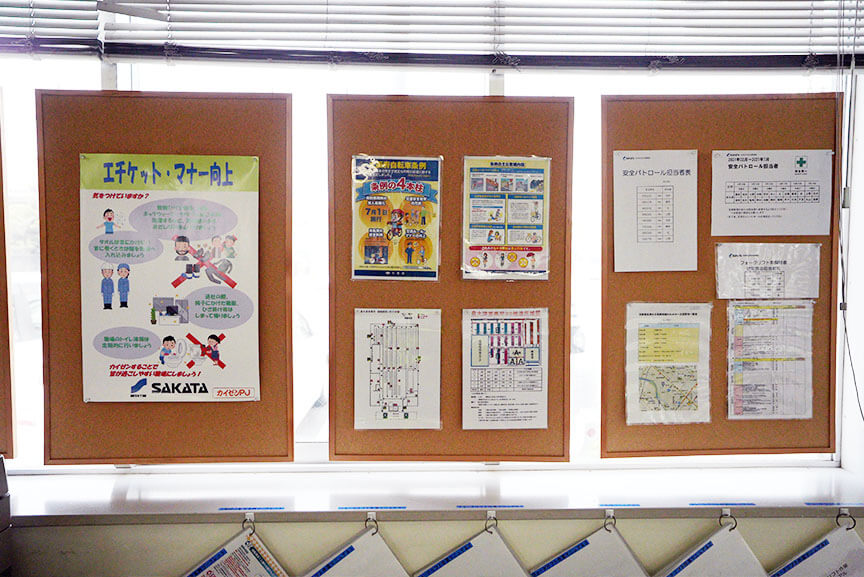
6.Quality control
As well as daily quality control, we will provide our customers improving logistics quality and services constantly by setting quality control goals, creating and executing work efficiency plan by PDCA.
(2)Compliance with the Pharmaceutical Affairs Law / Manufacturing work
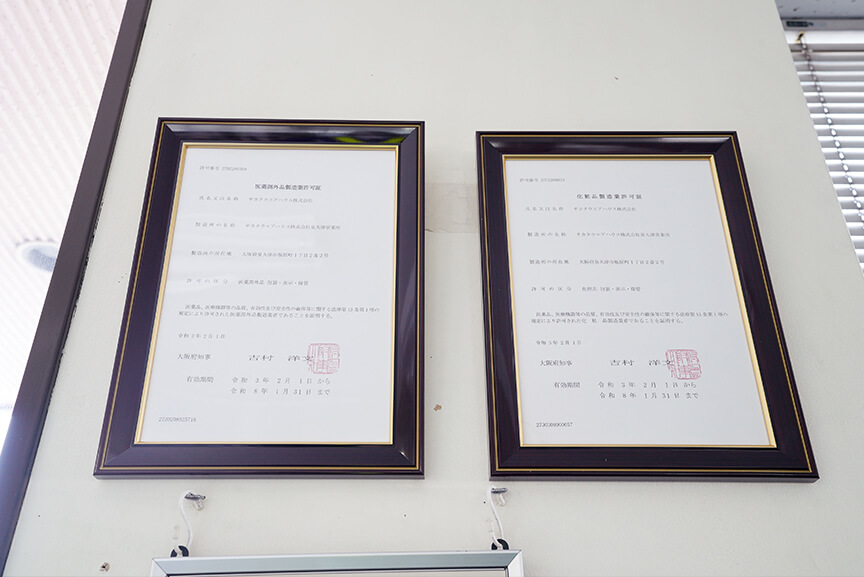
Manufacturing Permission (packaging, display, storage) of the Pharmaceutical Affairs Law
Warehouses with manufacturing licenses can perform manufacturing operations (packaging, labeling, storage) such as product appearance inspection, package replacement, and attachment of pharmaceutical labels/sealing of efficacy statements for imported cosmetics and quasi-drugs based on the Pharmaceutical Affairs Law, as well as the preparation of manufacturing records and operations/quality control by responsible engineers.
3PL Systems

Sakata Warehouse is promoting “systemization” and “visualization” of logistics to maintain and improve the quality of logistics by standardizing and streamlining operations, and to reduce errors to zero, by linking warehouse operations support tools such as the WMS and TMS core systems, cargo labeling system, piece picking system, and shipping inspection system, with the incoming and outgoing management, inventory management, and transportation and delivery management of electrical components, industrial machinery, and medical equipment.
We also provide high quality and accurate information services (fulfillment services) to our customers by using business support tools such as web-based ordering systems and shipping history management systems.
Overall picture of the 3PL logistics system (“standardization + efficiency + visualization” promotion)
System Introduction
Warehouse /DC list

Sakata Warehouse has distribution centers in the Kansai, Chubu, and Kanto regions, providing warehouse services and distribution center functions in compliance with the Pharmaceutical and Medical Devices Act for cosmetics, quasi-drugs, and medical devices, which are frequently requested by our customers.
We also provide BCP-compliant logistics services through the coordination/networking of our bases.
DC Quality Control

Sakata Warehouse has set up a department to implement company-wide quality control, and is working to maintain and improve total logistics quality by providing education, guidance, and support for 5S methodology and Kaizen at each sales office/logistics center, as well as coordination and collaboration among related departments.
In addition, we hold regular meetings with our customers to analyze the causes of accidents and complaints, take countermeasures, and report on Kaizen activities to enhance the relationship of trust with our customers, promote internal and external communication, and implement stable quality control.