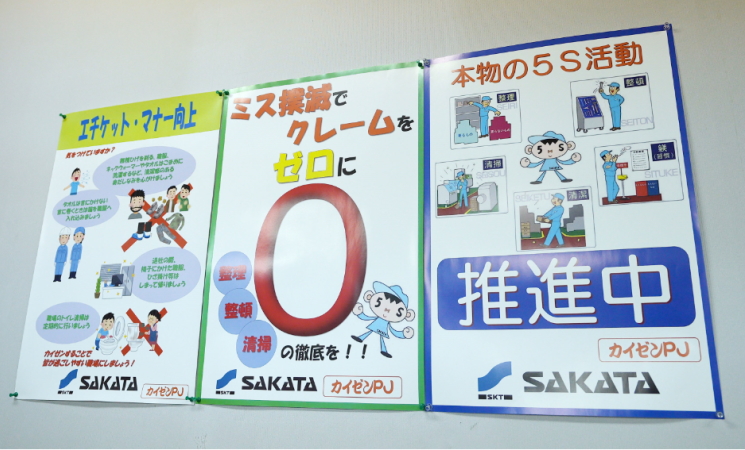
Sakata Group’s efforts to improve logistics quality
Guidelines for Sakata Group’s Logistics Quality Control Initiatives
“Continuous business improvement” and “Proposals to customers”
- Work on continuous “business improvement” in all business locations.
- If necessary, don’t hesitate to “do” traditional work and review it on a zero basis.
- We will make constant proposals to all customers and related parties.
Details of initiatives to improve logistics quality

1. Analysis and improvement through numerical understanding
|
a. Work errors in the warehouse
The number of work errors that occurred in the warehouse is counted. *Mistakes that were discovered before shipment and were immediately corrected are also included in the total.
b. Wrong shipment
Tabulates the number of cases in which a different product from the one ordered (shipping instruction) was shipped or a difference in quantity occurred.
c. transportation accident
The number of incidents of defacement, damage, late delivery, loss, etc. that occurred during transportation and delivery is counted.
2. Business improvement through PDCA cycle
We are continuing our efforts to improve operations by implementing the PDCA cycle at each sales office and team.
a. Plan
![]() |
[Setting of improvement targets] [Verification of results through continuation of improvement activities] |
---|
b. Do
![]() |
[Kaizen] ・ Examination and creation of improvement plans ・ Thorough correct work ・ ToDo list creation ・ Monthly activity record creation |
---|
c. Check
![]() |
[Problem raising / analysis] ・ Proposal to prevent mistakes ・ Immediate response when a mistake occurs ・ Investigation of the cause after a mistake occurs |
---|
d. Action
![]() |
[Confirmation / verification of improvement results] [Information sharing of identified issues and improvement measures] |
---|
3. Raising awareness within the company
At Sakata Warehouse, we are actively working to raise awareness of quality control within the company.
![]() |
a. Promotion of 5S
We are constantly promoting the thoroughness of 5S in our warehouse. |
---|
![]() |
b. Monthly poster display
Each month, we post posters with items that we need to be aware of, such as “tidiness,” “cleanliness,” and “greetings,” to ensure that all employees are aware of them. |
---|
4. Implementation of mid-career employee training
Sakata Warehouse provides mid-career employees with education on standard management and operation methods for operating a distribution center as one of the skills required for quality control.
(Example of education and training implementation)
a. Education on standard operation management contents of WMS (arrival-storage-shipping / transportation / delivery management) and inspection system
b. Understanding of standard indexes for logistics work productivity and education on calculation methods
c. Education on income and expenditure management methods for each shipper
d. Training on how to find improvement points in the warehouse and improvement methods
e. Holding of debriefing sessions on 5S/quality control initiatives at each sales office
5. Efforts to improve quality with shipper companies
![]() |
At Sakata Warehouse, we regularly provide feedback to shipper companies through visits and reports on 5S initiatives and quality improvement activities. As a result, we are building a system to work on quality improvement together while communicating with the shipper company. |
---|
“All Japan Logistics Improvement Case Conference 2009” Awarded the 23rd Outstanding Case Study

|
|
The photo above is the award I received at that time.
The photo below shows our company Watanabe giving a lecture entitled “Quality Improvement Efforts Aiming to Realize CS / ES -Challenge to” Zero “Logistics Mistakes by Utilizing Information-“.
Date: April 23, 2009
Presenter: Sakata Warehouse Co.
Masaru Watanabe, Assistant General Manager, Sales Operations Department
Introduction of quality control efforts at sales offices

At Sakata Warehouse, quality control is thoroughly implemented at each sales office. By conducting quality control at each sales office, we have created an environment where each employee working in the field can think independently and devise ways to improve. As an effect of this, we have been renewing our quality year after year, which is very high in the industry.
Examples of Efforts to Improve Quality at the Izumiotsu Sales Office
1. Grasp the current warehouse figures and consider improvement measures
![]() |
We grasp the current situation in the warehouse numerically. By continuing this initiative on a monthly basis, we have a system in place to take trends and improvement measures. |
---|
2. Quality improvement status / numerical value by CS activities
![]() |
Every year, we quantify the opinions of our customers to understand the trends and use them for further improvement measures. |
---|
3. 5S Initiatives / Warehouse Inspection
![]() |
We have created our own 5S checklist and everyone checks it on a weekly basis. In addition, depending on the results, the internal committee will further check the yellow card checklist, improve it, and report on it to ensure thorough inspection of 5S and the warehouse. |
---|
4. 5S Initiatives / Promotion Status Posting
![]() |
As part of our 5S efforts, we are continually working to raise awareness of each employee by posting information on the progress of 5S at our sales offices. The main contents of the notice are as follows. ・Number of consecutive days of incorrect shipment “0” ・Criteria for organizing locations ・Status of 5S Promotion ・Example of 5S improvement |
---|
5. Report on annual activity results
![]() |
We constantly monitor the results of our 5S efforts on a yearly cumulative basis. By ensuring that all employees are aware of the 5Ss on a daily basis, we are able to raise awareness of quality improvement among each and every employee in the workplace. |
---|