第239号物流現場生産性向上への取組み(2012年3月8日発行)
執筆者 | 五十山田 俊 (株式会社チームTP 取締役 シニアコンサルタント) |
---|
執筆者略歴 ▼
目次
1.はじめに
一般に、物流現場の生産性を論じるとき、コストをキーとなる指標として分析し、その低減を図ることが多い。ABC(活動基準原価計算)を導入し、コスト改善の効果の高いアクティビティを洗い出して改善することが、多くのロジスティクス企業で行われている。コストにかかわる指標として、輸送における積載率、復荷率、保管における坪当たり保管容量、荷役における時間当たり格納・ピッキング件数等が管理されている。また、作業品質の指標としては、誤品率、欠品率を管理し低減活動が行われている。
しかし、コストを低減するということから前述の指標に管理の目は向けられているが、具体的にどうやってこれらの指標を良くするのかはあまり論じられていない。本稿では、物流現場の庫内作業に絞った生産性向上の取組について述べる。
2.すべての現場の基本は3区分管理と5S
(1)3区分管理
「3区分管理」は物流現場だけでなく、モノづくり現場、事務作業現場、技術作業現場等、すべての現場に共通する原則である。これができていないと、後述の「5S」もできないし、改善に手がつけられない。
3区分管理とは、執務場所を「通路」「保管場所」「作業場所」の3つに明確に区分し、管理することである。
① 通路
通路は人と物が移動するために設けられる。作業者、管理監督者、参観者・・・、台車、フォークリフト、トラック・・・が移動するために設けられるが、もうひとつの機能がある。通路は、執務場所の「保管場所」と「作業場所」を区画する機能も持つ。通路の原則は以下の通りである。
・直線で交差は直角。(見通し良く、区画が長方形になるように)
・目的に応じて十分な幅を取る。
(人と台車だけなのか、フォークリフトが通るのか)
・通路に物を置かない。通路で作業しない。(邪魔で通路の機能を損なう)
・白線等ではっきりと分るように線引きする。
② 保管場所
物を保管する場所である。物流現場では荷を保管する場所である。モノづくりでは、「ストア」と「ストレージ」であり、事務作業ではファイルロッカーであったり、机の引き出しであったりする。保管場所の原則は以下の通りである。
・十分な広さ(大きさ)をとる。(収納物が溢れ出ない)
・間口は広く、奥行きは浅くする。(芋掘りや積替えをなくす)
・整理(不要なものは追い出す)整頓(必要なものが直ぐ取り出せる)を徹底。
・何が保管されているかわかるようにする。(表示)
③ 作業場所
何らかの作業をする場所である。物流現場であれば、荷捌き、梱包、検品等を行う場所である。モノづくりであれば、加工・組み立てを行う場所で、事務作業であれば事務机の上である。作業場所の原則は以下の通りである。机の上が書類であふれかえっている事務作業現場はもってのほかである。
・作業に必要ないもの(部材、工具、書類)を置かない。
(今必要な物以外は邪魔になる)
・必要な物が直ぐに使えるように配置する。(手元配置)
・作業は1つ1つやりきる。同時に2つの作業はやらない。
(お店を拡げず、ミス防止)
<図1>3区分管理
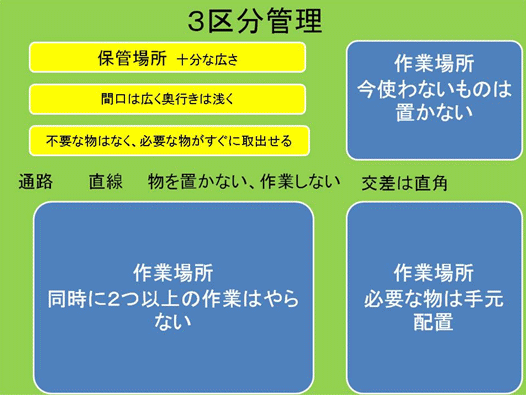
(2)5S
5Sはご存知の通り、整理、整頓、清潔、清掃、躾である。3区分管理がきちんとできた状態で、5Sを推進する。5Sの定義は省くが、要するに不用品は現場から追出し、必要な物がすぐ取り出せるようにし、職場がきれいでわかりやすく、それを維持する仕組みがあって、人がそれを理解し実践することである。3区分管理の徹底と、5Sで現場の生産性はかなり上がる。
海外企業に行くと、よく作業者から「5Sなんてむだなことをなぜやらせるのだ?そんなことをやっている間に、仕事した方が良い。」という言葉を聞く。日本人の管理者がそれを説得できなくて、何とか理解させてくれという依頼を受けることがある。管理者が5Sの意義をきちんと理解していないため、説得できないのだと思う。
そんな場合は現場で、5Sが崩れている実態を前にして、いかに効率が悪いかを体験させる。整理整頓ができていなければ、不要なものをどけなければならない。芋掘りや置き換えが発生する。整頓ができていなければ、探しのムダが発生する。実際に何かを取り出せて、そのとき、5Sができていないから発生するムダ作業を指摘すると、ほとんどの場合納得してくれる。 3区分管理と5Sは現場の基本である。何事にも優先してこれらを確立させなければ、どんな施策を採っても効果は期待できない。
3.生産性向上のための作業分析
(1)作業の分類(付加価値に注目して)
物流の庫内作業は、作業者の「動き」で構成される。動きは大きく「作業」と「ムダ」に分けられる。さらに、作業は付加価値をつける「働き」=主作業(正味作業)、と付加価値のつかない作業に分かれる。付加価値のつかない作業は大きく付随作業と余裕に分類する。
<図2>物流現場作業者の動きの分類
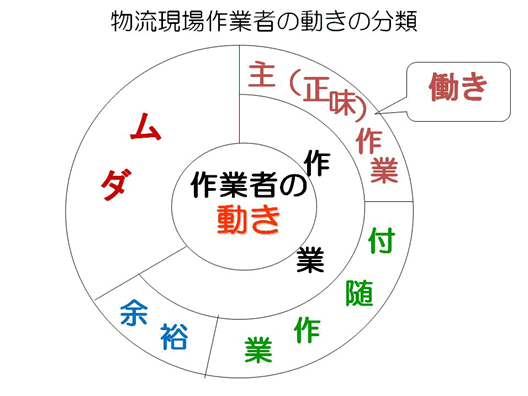
以下に作業分類を解説する。
① 主作業(正味作業)
工程を前に進め、付加価値をつける作業。庫内作業では、ピッキング作業で、差立てからピッキングリストをとる、棚から商品を取って箱に入れる、梱包する、ラベルを貼る等がある。お客様からお金をもらえる作業と考えれば判断し易い。
② 付随作業
主作業に伴って発生し、その作業自体は付加価値を生まないが、現在の作業条件では主作業を成立させるためにどうしても必要な作業である。パレットの準備・片付け、庫内整理、はい替え、設備の点検、検品作業、移動、帳票の取扱い等がある。作業の準備はすべて付随作業となる。
③ 余裕
職場管理上必要なものと、作業者の疲労回復・用達しのために行うものがある。職場管理上必要なものとして、朝礼、打ち合わせ等があり、疲労回復・用達として、休憩、体操、水飲み、トイレ、喫煙等がある。
④ ムダ
まったく不要な動きである。本来であればやらなくてすんだ作業も含まれる。作業者の手待ち、商品探し、場所探し、芋掘り、邪魔なものをどける、作業のやり直し、誤出荷の処理、指示不徹底のために発生する用談等がある。厳しく見ればいろんな「ムダ」を見出すことができる。
(2)IEによる作業分析
<図3>IE手法体系
*画像をClickすると拡大画像が見られます。
IE分析手法の概略体系は<図3>に示す通りである。それらの中で、初心者でも短時間の教育で理解でき、物流現場のムダを簡単に炙り出す手法として、工程分析と、簡易ワークサンプリング法を使うことを勧めている。この2つの手法で、問題点と改善の方向付けをして、必要ならば、専門的技量を必要とする時間分析やワークサンプリング法を行い問題の深堀をするとよい。
4.分析を生産性向上に結びつける
① 工程分析
工程分析は入荷から出荷までの商品の流れ、仕事の流れを工程の要素別に記号を用いて分析し、その内容や相互の関係を調査研究する手法である。物の流れを対象にする製品工程分析と、仕事の流れを対象にする作業者工程分析の2種類がある。製品工程分析では工程を「加工」「検査」「運搬」「停滞」の4種類の工程に分けて分析する。この分析では、荷物が何もされずに放置されている停滞と運搬距離・時間の長さが浮かび上がってくる。ただムダに時間が過ぎていることと運搬のムダが定量的につかめる。作業者工程分析は作業者の工程を「作業」「検査」「移動」「手待ち」の4つに分けて分析する。何もしないでいる手待ち時間のムダや、移動距離・時間の長さが浮かび上がってくる。そして、物と作業者の動きをレイアウト図の上に記入する(動線分析)。
工程分析では、停滞・手待ちという作業管理に起因する問題と、運搬・移動という庫内レイアウト、商品の配置の問題が浮かび上がる。これらの問題を改善し、同じ手法で、その効果を確認することができる。
② 簡易ワークサンプリング
本来のワークサンプリング法は複数の作業者の主作業、付随作業、余裕、ムダの比率を定量的に調べ上げ、改善に結びつける有効な分析手法である。しかし、前準備作業が必要で、サンプリングポイント数も多くとらなければならないので、初心者には不向きである。
そこで、ワークサンプリング法を大幅に簡易化し初心者でも短時間に現場の問題点を把握し、改善の方向付けをする手法が考えられた。サンプリング間隔にランダム時間を使わないで、30秒もしくは1分間隔でサンプリングを行う。サンプリング点数は60点~120点とし、観測時間は30分~2時間ですむ。
観測対象作業者を決め、作業を少し見て、その作業者の主作業、付随作業、余裕、 ムダを大まかに把握する。そして、決められたサンプリング時間間隔で、その一瞬の作業を見て、要素作業単位で記述する。その要素作業を、主作業、付随作業、余裕、ムダに分類する。サンプリング全数に対する主作業、付随作業、余裕、ムダの比率を算出する。付加価値のない「ムダ」そして「付随作業」に注目して、どうしてそれらが発生するのか「なぜ?なぜ?・・・」繰り返して、原因を特定し改善案を考える。そして、改善を実行する。
<図4>簡易ワークサンプリングで主作業率を挙げた事例
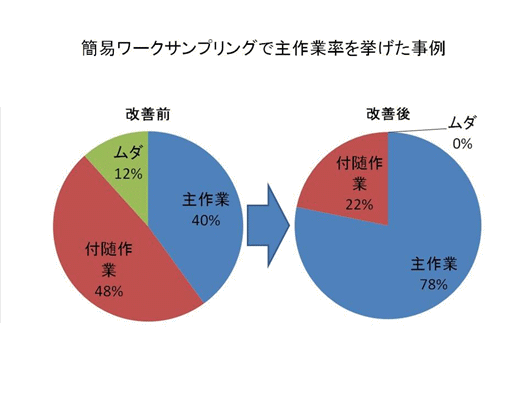
5.最後に
IE分析は専門家が行う難しいものと考えられる方が多いが、本稿で紹介した2つの手法は、比較的短時間で習得でき、簡単に現場の問題点を見つけて改善の方向付けができる。そのため、庫内作業のフォアマンや改善マン候補者に教育することが望ましい。
参考文献:
・トヨタの現場管理 日本能率協会編
・現場のIEテキスト(上)(下) 石原勝吉著、日科技連出版社
・ビジネスキャリア検定試験標準教科書 中央職業能力開発協会編
・ロジスティクス管理(2級)(3級)
・ロジスティクスオペレーション(2級)(3級)
以上
(C)2012 Shun Ikaida & Sakata Warehouse, Inc.