第270号明日からでも実施できる物流改善(2013年6月25日発行)
執筆者 | 平野 太三 (有限会社SANTA物流コンサルティング 代表取締役社長) -物流改革コンサルタント Dr.SANTA- |
---|
執筆者略歴 ▼
目次
1.1日500円の物流改善
物流改善が注目され始めてから20年を経過しているが、まだまだ物流改善が進んでいるとはいえない。物流グループ内(例えば、ピッキングチーム、配送チーム、流通加工チーム等)の改善、もしくは物流部門全体での改善は進みつつあるが、他部門や得意先にかかわる物流の問題は手つかずの企業も多い。その代表的な例としては「過剰サービスの見直し」「過剰在庫削減」である。この様な問題点は全社参画のプロジェクトを作って取り組まないと改善がなかなか進まないことが多い。今回はこの様な大きなテーマではなく、明日からでも実行できる小さな改善の進め方を紹介したいと思う。
しかし皆様の中で、「小さな改善と言っても過去継続して取り組んできたので、残されている問題はほとんど無い」と思っている方も多くおられるのではないかと思う。私は「毎日発生する500円の物流改善のネタ」を数多く見つけることを皆様に問題提起したい。1日500円の物流改善と言ってもバカにはできない。1年を仮に200日とすると毎日積み重なれば1年で10万円の改善になる。また、私の経験則では物流の問題点は、物流改善が進んでいる企業でも最低でも100個、物流改善が進んでいない企業では200~300個は存在する。10万円の改善ネタが仮に100個あれば、年間1000万円の物流コストが削減できる可能性があることになる。(図1)
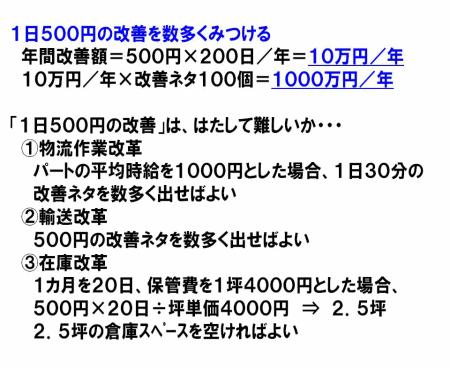
物流コストは、「物流人件費」「輸送費」「保管費」「包装資材費」「情報システム費」「水道光熱費」等、さまざまな経費が考えられる。
物流人件費の改善手順は後でじっくりと解説するので、まずは輸送費の削減手順を解説したい。1ケース当りの運賃をいかにして10円削減できる問題をみつけるかを考えることになる。例えば運送会社の集荷時間を見直すことで、1ケース当りで10~50円の運賃が削減する方法が考えられる。運送会社により集荷時間が違うが、早い集荷時間の運送便に間に合わずにやむを得ずに運賃が高くなったという事は無いだろうか? その対策方法としては「当日出荷受注締め時間の厳守」「受注処理時間の短縮」「出荷処理時間の短縮」「ピッキングの優先順序の見直し」「送り状発行のスピードアップ」等の対策が考えられる。これにより「1ケース当り20円の削減が25個(例えば5個口×5件)」が実現できれば1日500円の改善が見込める。他の輸送費の改善ネタには、「得意先による運送会社指定の見直し」「誤出荷削減による返品運賃の削減」「横持ち移動費の削減」「運送会社の見直し」等色々ある。ここでは詳細の解説はしないが、解決する方法はあるのでよく検討して欲しい。
2.物流作業を分解すると改善の可能性が見えてくる
それでは1日500円の物流改善ネタを作業改革で例にあげて、別の指標で置き換えてみたい。500円を物流作業時間で置き換えると、パートの時給を1000円とした場合、物流作業時間の30分に該当することになる。物流業務は1人で行っていない場合が多いから、これを業務別人数で頭割をしてみると更にわかりやすい。仮にピッキング人数が10人であったとする。計算式としては「1日30分÷10人=3分/人」となる。1人当り1日平均3分の改善が実現すれば、ピッキング業務での物流改善金額が年間10万円になるのである。更に、ピッキング行数や伝票枚数で計算すると具体的な目標が見えてくる。1人当り1日で300行ピッキングし、1伝票の平均行数が4行とすると、「1人当り1日3分(180秒)÷300ピッキング=0.6秒/ピック」、「0.6秒/ピック×1伝票4行=2.4秒/伝票」になる。(図2)
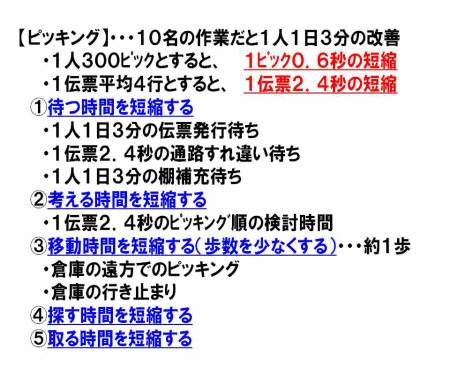
皆様の物流センターで、「私の物流センターでは1回のピッキングで0.6秒を短縮できる余地が全くない!」と言い切れる方が果たしておられるだろうか? 言い切れるということは根拠が必要である。ありとあらゆる改善をやりつくし、物流メンバーの意識が高度なものでないと達成できないと思う(私の経験則では意識・意欲だけで20%の効率は変わる)。これを更に詳細に問題点を具体化して考えてみることにする。
3.物流作業の5つの無駄
物流作業には5つの無駄(「待つ無駄」「考える無駄」「移動する無駄」「探す無駄」「取る無駄」)がある。この5つの無駄の視点でピッキングで「平均0.6秒の改善/ピック」「平均2.4秒の改善/伝票」「平均3分の改善/人」のいずれかを実現できる無駄な作業が無いかを探すのである。
1つ目は待つ無駄な時間。出荷伝票(ピッキングリスト)が発行されず、待っていることは無いだろうか。出荷伝票がバッチ発行で1日3回発生していれば、1回当り平均で1分待てば500円の改善ネタを見つけたことになる。出荷伝票を発行していても、指示待ちであった場合も該当する。また、棚間通路が狭く、1伝票当りで2.4秒のすれ違い待ちが発生していても同様である。1回当りのすれ違い待ちが10秒であれば、4伝票に1回発生していても同じ無駄が発生したことになる。棚欠品も物流作業の待ち時間のひとつである。棚欠品が発生すればピッキング時に棚に商品が無く、バックヤードから商品を補充されるのを待つ必要が出てくる。この待ち時間が1回当りで6分かかっていたとすれば、1人当り2日に1回発生していれば年間10万円の改善ネタ、毎日発生していれば年間20万円の改善ネタになる。
2つ目は考える無駄な時間。ベテランであれば該当商品がどこにあるか大体わかっているので、出荷伝票をひと目みただけで歩く歩数が一番少ない順番がわかる。この順番を決める時間も数秒はかかるため、これも改善ネタになる。これが新人であればベテランの数倍の時間はかかる。ピッキングの順番以外にも、「得意先や商品により出荷方法が変わる」「運送会社の出発順によりピッキング順序が変わる」等の判断業務も考える無駄に入る。
3つ目は移動する無駄な時間。ピッキング業務時間の約半分は移動する時間である。物流センター内のピッキング効率は、1時間当り60~80ピックが多い。仮に1時間当り60ピックとすると、1回のピッキング時間は「1時間(3600秒)÷60ピック=60秒/ピック」である。1ピック60秒の中で0.6秒~1秒の短縮方法としては、「出荷件数(ピッキング回数)の多い順に商品を並び替える」「出荷大量品を出荷検品エリアの近くに配置する」「ロケーション表示をする」「ピッキングリストを発行するプリンタをピッキングエリアに近付ける」等、色々ある。移動する無駄な時間は、0.6秒どころでなく、数秒単位の改善ネタがあるためよく検討して欲しい。
4つ目は探す無駄な時間。「ピッキングする商品の置き場所がわからない」「商品のロットNoの確認に時間がかかる」「横に似た商品が並んでいるため確認行為に時間がかかる」等が無駄な時間にあたる。改善方法として、「表示方法の見直し」「似通った商品をバラバラに配置」等の対策を実行すれば、効果がでることが多い。
5つ目は取る無駄な時間。物流センターでは保管効率を向上させるために、高い棚の設置、パレット積み(またはネステナー積み)をしている企業が多い。ピッカーの手が届かない棚であれば、台を取りに行く時間が余計にかかる。パレット積みの場合は手が届かない場所にあればフォークリフトを使用して出荷効率が1/3以下になる。この対策は、不要・不急品は保管効率を優先し、よく出る商品は作業効率を優先する保管方法にすれば効果が出る場合が多い。
この様な手順で、受注、入荷、流通加工(シール貼り、セット組み、袋詰め等)、出荷検品、送り状作成、補充等も同じやり方で無駄が無いかを作業分解して、考えていけば良いのである。
4.物流センターのレイアウトで無駄を見つける
無駄を見つける他の方法として、倉庫レイアウト図を作成することも必要である。物流業務別に人の流れを図面で追いかけると問題が見えてくる。(図3)
ピッキングリストはどこで発行しているのか? 保管エリアのすぐ近くに置いていれば、移動する時間が短縮できる。図3の場合であれば、右端にピッキングリストを発行するコンピュータが置いているから、中央部に移動することが出来れば1年で何十万歩の改善ができるかもしれない。
棚間通路の行き止まりがあれば、戻りが発生するため歩数が長くなる可能性が高い。この課題は少し難しいが、通路を確保せず保管効率を優先するか、作業効率(通路幅を確保せず保管効率が悪くなるがそれ以上に効果が出れば良いという考え)を優先するか、の選択になる。
物流改善ネタが少なくとも100個以上あるということを申し上げたが、ご理解頂けたであろうか。物流現場には1日当り500円以上の改善ネタが山の様に埋もれているのである。「物流改革は駄目であれば元に戻したら良い」というものも多い。失敗を恐れずトライして頂きたい。また、結果検証をすることも忘れない様にして欲しい。結果検証の中でまた新たなアイディアが浮かぶことが多いからである。
以上
(C)2013 Taizo Hirano & Sakata Warehouse, Inc.