第174号物流作業改革で無駄な人件費の削減(2009年6月23日発行)
執筆者 | 平野 太三 有限会社SANTA物流コンサルティング 代表取締役社長 -物流改革コンサルタント Dr.SANTA- |
---|
目次
1.物流作業改革の考え方
近年、企業の売上が減少する中、社員切り、派遣切りが問題として扱われているが、物流が本来目指すべき姿は、「物流品質の向上と、売上の増減に対応できるコストパフォーマンスが良い物流体制の構築」であると思う。それを実現する上で物流改革が必要になる。物流改革には、「物流クレーム改革」「在庫改革」「物流作業改革」「輸送改革」「組織改革」等がある。さまざまな物流改革の中で今回は「物流作業改革」をテーマに解説したい。
あらゆる改善活動に共通していることであるが、まず最初にやらなければいけないことは、出来るだけ多くの問題点を出すことである。問題の種類も色々あり、現在メンバーが気付いている問題、メンバーが気付いていない問題、現在は大きな問題では無いが将来に発生が予測される問題(将来問題)がある。将来問題とは、「ベテランの配送担当者が3年後に定年で退職するため、何も手を打たないと最適な配送ができなくなる」という様な問題を言う。また、問題を発見する方法も色々とある。経験則で発見する方法、他社と比較して見つける方法、業務の流れで発見する方法、得意先を特定して発見する方法、時期を限定して発見する方法、数値化をして発見する方法、等がある。
この中で数値化をして問題を発見する方法をお薦めしている。入荷、ピッキング、検品等あらゆる業務で、現在効率が良い仕事をしているかを全体、及び個人別に算出するのも数値化をして発見する方法の例である。ただ、数値で把握することは理論的には正しいと思っても、現状の効率状態を把握している企業は非常に少ない。皆様の企業では、今日のピッキング効率は全体ではどうだったか、個人別ではどうか、入荷の作業効率はどうか把握ができているだろうか。その例外として、ピッキングに関しては、ハンディターミナルを使用してバーコードでピッキング検品を行っている企業では個人別の作業効率を取ることが可能であるが、物流全業務で把握している企業はほとんど無いと思う。それではどういう手順で物流作業改革を進めたら良いのであろうか。
2.物流作業改革の手順
私が推奨している物流作業改革の手順は以下の通りである。図1をご覧頂きたい。
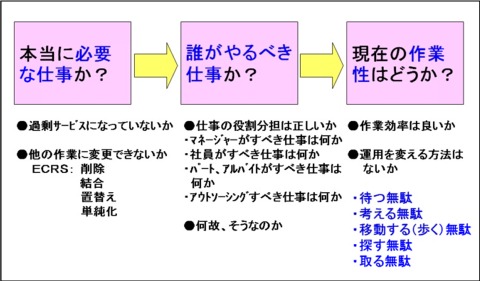
図1 物流作業改革の視点
まず最初に考えなければならない事は、「不要な仕事をやめる」ことである。コンサルティング時にこの様な話をすると、必ずと言って良いほど「私のセンターでは不要な仕事はしていません」という答えが返ってくる。不要な仕事の例としては、「お客様が望んでいないのに顧客サービスと思い込んで納入明細(ダンボールの中に入っている商品の明細書)をつける」「在庫精度が悪い(コンピュータ在庫と実在庫の差異が発生)ために、毎朝、品薄商品の実在庫を確認してホワイトボードに記入する」「物流クレームが多く、対応に時間がかかる」等が挙げられる。この様な仕事は必ずやらないといけない仕事では無いため、やめる対策をたてなければならない。物流では過剰サービスが目立つ。過去からお客様から要請があったため、それを継承しないといけないと思い込んでいる場合が多い。例えば前述した「納入明細」の問題でも、ケース単位で発注して在庫を豊富に持っていた時代であれば、急ぎの商品と急ぎでない商品を区分けして入荷処理をする必要があったため、納入明細の必要性があった。ただ、在庫削減を推進して出来るだけギリギリの在庫を持つ時代では、入荷するものはすべて急ぎの商品になる。その様な企業では、内容明細を見なくなる場合も多々ある。よって、仕事をそのまま続けるのではなく、何のためにその仕事をするのかをよく考えておいた方が良い。
次に検討すべき事は、仕事の役割分担である。物流ではマネージャー、一般社員、パート、派遣社員等の様に給与体系が違う。時間当りの給与が違うのであれば、給与が多い人は何らかの仕事の付加価値がなければ意味がない。「他のメンバーに無い知識」「他のメンバーに無い技術」「他のメンバーに無いスピード」のいずれかが必要になる。ただ、物流業務のスピードに関しては、パートの時間当りの給料の3倍をもらっているからと言って、3倍のスピードで仕事ができるかと言えばそうでない。逆にベテランパートの方が、ベテラン社員のピッキングのスピードより早いという現象もよくみかけることである。よって、専門知識が不要な単純作業であれば、時間当りの給与が低いメンバーに仕事を移管する必要がある。それができない原因分析をし、対策をたてることにより単位時間当たりの人件費が削減することができる。役割分担が実現出来て、初めて作業効率を検討すれば良いのである。
3.物流作業の現状把握
物流現場の状況を把握していない企業がほとんどであると申し上げたが、簡単に物流作業の傾向を掴むことは可能である。図2の週間作業集計表をご覧頂きたい。
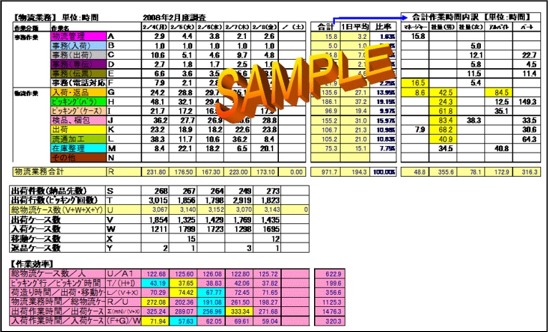
図2 週間作業集計表
物流の作業効率を掴むためには、作業時間と作業量の2つが必要である。作業時間は物流メンバー全員に15分単位で自己申告をしてもらい、集計する。作業量は、出荷行数、出荷ケース数、納品先件数等を調査する。作業時間と作業量がわかれば、比較をすれば作業効率が見えるのである。このデータを連続した1週間で調査する。これは、曜日変動の傾向を掴むために必要である。例えば、「全体のピッキング行数÷全体のピッキング時間」で、1時間当りの全体のピッキング行数が算出できるが、実際データを取ってみると曜日により大きな差が発生することがある。この発生理由を原因分析し、「作業負荷が少ない仕事量であれば、開始時間をずらしたり、人数を削減したりして無駄な作業時間を調整する」という方法を取ればよい。また、職能別に作業時間を集計することにより、社員が付加価値の低い仕事をしていないいか、何故そうしなければならないのかを原因分析できる。
私もこの手法を確立するまでに試行錯誤をしたが、15分単位の集計が一番良いと思う。1分単位に正確に時間を計測する方が望ましいかもしれないが、細かくデータを収集することによる物流現場の負荷、集計する人の負荷を考えると、最終的にこのやり方が良いと判断した。私はこのやり方で20%程度誤差が発生しても良いという感覚で考えている。今、説明しているのは、正確なデータを取ることが目的では無く、数多くの物流作業の問題をみつけることが目的である。もっと、改善業務を絞り込んだ段階で、正確なデータを取れば良いと思う。ちなみに、物流現場が40人程度の現場であれば、2日あれば週間作業集計表は完成できるので、一度トライして頂きたい。
4.物流改革の効果予測
今後、物流作業改革の改善策で、簡単でしかも効果が大きいものはまず無いと思う。今後は、「小さな改善の積み重ね」「難易度の高い改善」「お金のかかる改善」を実行していかなければならない。「小さな改善の積み重ね」というのは、例えば1日500円の効果を伴う改善策を数多く行う。1日500円と言っても、1年を仮に200日とした場合、年間10万円になる。私の経験則では、物流現場には100~300個の大小の問題をかかえている。それが正しいとするならば、10万円×100個=1000万円になる。「難易度の高い改善」とは、お客様に依頼したり、共同物流を実現したり、他部門や他企業を巻き込んだ改善である。確かに難易度が高いため、10個実施して1~2個実現したら良いという感覚で考えて頂きたい。今までやれなかったことを成し遂げるのであるから、その効果は大きく、年間数百万円の効果を出すことも少なくない。これを行っている企業と、行っていない企業とでは、数年後に大きな差ができる。何故ならば、物流改革で得た金額を、借入金の返済、社員の待遇の改善、商品開発への投資、販促への投入など、さまざまな対策を数千万円単位で投資できるからである。
「お金のかかる改善」とは、コンピュータシステムの導入、物流機器の導入等、大幅なコストを投資することで、投資を上回る効果を実現する方法である。「小さな改善の積み重ね」「難易度の高い改善」は、やってみて万一うまくいかない場合は元に戻せば良いが、何百万円も投資をした後で駄目だからと言って返品はできない。よって、改善をすることで、どのくらい効果が出るのか、また本当に予想通りの効果あるのかを仮説検証しなければならない。図3をご覧頂きたい。
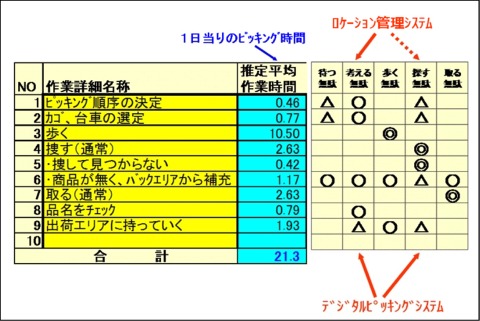
図3 物流作業改革の効果測定
ピッキング業務を更に詳細に細分化し、全員の合計時間を分割したものである。物流作業の中には、「待つ無駄」「考える無駄」「移動する無駄」「探す無駄」「取る無駄」が入っている。物流作業改革は、この無駄取りをしながら作業効率を上げていくのである。
仮に、ロケーション管理(商品の置き場所の管理)システムを導入し、ピッキング効率を向上することを目的で、300万円費用がかかるとしよう。5年償却として月額5万円の費用が毎月発生するので、人件費だけで効果を出すとすればシステム導入後に5万円以上の人件費が削減しなければならないことになる。ピッキングでパートが10名で1名の概算人件費が月額8万円とすれば、5万÷80万=6.25%。10名×6.25%=0.625人。よって、約0.6人減で、6.3%の効率アップが採算分岐点となる。それでは、ロケーション管理システムで、6.3%の効率アップの検証をどうするかということになるが、「ロケーション管理システムの効果」は、「探す時間の短縮と考える時間の短縮」が予想される。その時間に対してどの程度効率アップできるのかを検証すれば、より正確な効果予測ができる。この様な考え方で、お金がかかる改善の検証をすれば、思っていたほど効果が無かったということが無くなると思う。
以上
(C)Taizo Hirano & Sakata Warehouse, Inc.