Manufacturing service (fulfillment service)
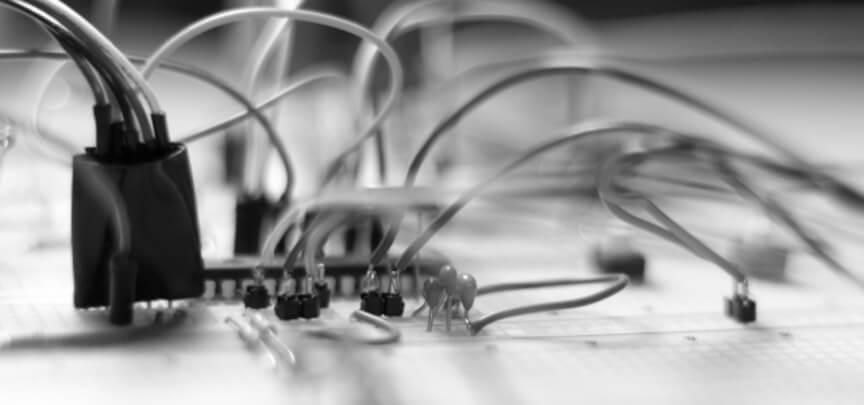
promote total quality control, operational efficiency,
and cost reduction with 3PL services, including
inspection, repair, BTO, and other operations.
The Sakata Group provides a comprehensive fulfillment service that provides (1) cosmetics, (2) electronics, industrial, medical equipment, (3) pharmaceuticals, toiletries and other industries with the functions required by customers by providing information, manufacturing and distribution services in addition to warehouse and 3PL services.
Overview of Fulfillment Services
The overall picture of “Fulfillment Services” (information, manufacturing, and distribution services) is summarized below.
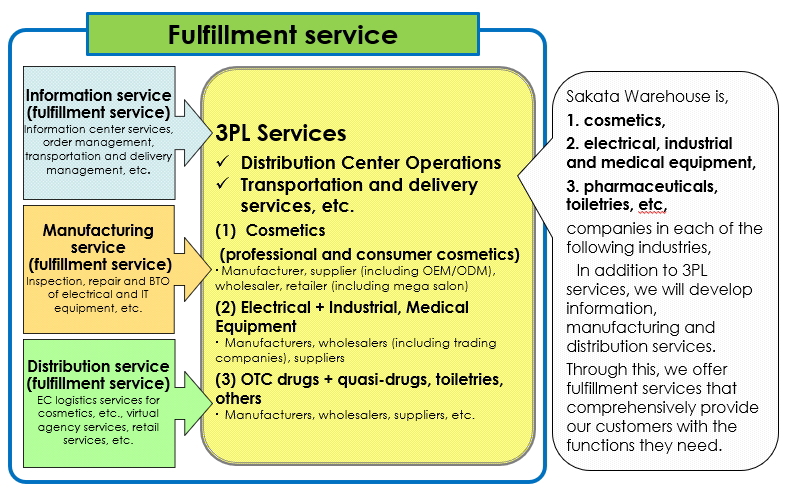
Manufacturing Services

Sakata Warehouse’s Manufacturing Service – Fulfillment Services – provides companies in the electrical and industrial equipment industry with total quality control, operational efficiency and cost reduction through warehouse, 3PL services, inspection, repair and BTO services.
“Manufacturing services” for electrical and IT equipment, etc.

inspection
- When accepting the finished product in the warehouse, we will check if there are any problems in appearance and operation.
- If used in conjunction with our warehousing and 3PL services, you can expect to reduce the cost of transportation from the inspection facility to the warehouse.
- We have experience in visual inspection, disassembly inspection, dielectric strength inspection, and operation inspection of industrial machinery.
repair
- Repairing faulty products at the request of customers.
- Taking advantage of the warehouse and 3PL service, you can rely on the entire process of receiving, repairing and returning returned products.
BTO(Build To Order)
- When accepting the finished product in the warehouse, we will check if there are any problems in appearance and operation.
- If used in conjunction with our warehousing and 3PL services, you can expect to reduce the cost of transportation from the inspection facility to the warehouse.
- We have experience in visual inspection, disassembly inspection, dielectric strength inspection, and operation inspection of industrial machinery.
By providing it together with logistics operations, we will reduce the waiting cost of workers and the work load of your company.
We can also respond flexibly to sudden increases in workload and emergencies.
Please contact us for advice on how to improve your business as well as new business. We will be happy to make suggestions.
Operation example related to manufacturing service / BTO

The following is an example (issue and solution) of how to deal with embedded products (Build To Order) in manufacturing services.
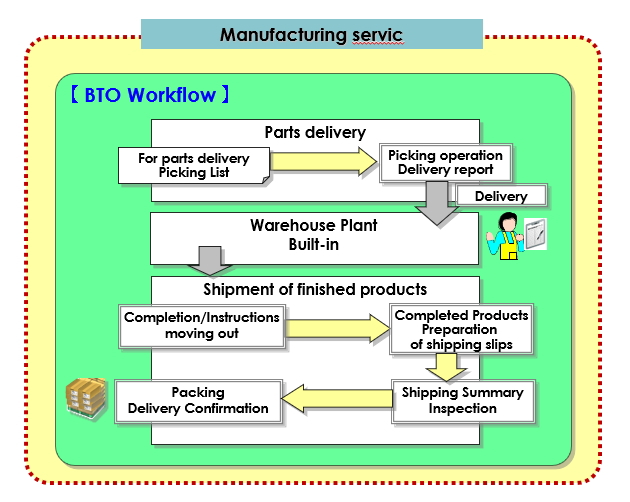

- Difficult to manage product numbers due to the huge variety of finished products
- Traceability was difficult because the data of delivered parts was not linked to the data of shipped finished products. (It took a long time to respond to inquiries about finished products.)


- When the following method is adopted, the part number is set to order number of the finished product. The limits of management have virtually disappeared.
- Create shipping slips for finished products using the barcode on the processing instructions as a key. This eliminates the need to link the parts delivery slip with the finished product shipping slip, and saves a great deal of time. (History search is also possible.)
Features of manufacturing services

The features of Sakata Warehouse’s “Manufacturing Service” – Fulfillment Service – for customers (companies) in the electrical machinery and industrial equipment industries are shown below.
◆Acting as an inspection agent and quality control at the time of product acceptance
By setting up inspection rooms in warehouses and conducting visual inspections by sampling lots, and product assembly and continuity inspections, it is possible to reduce man-hours and costs for moving to inspection facilities and to improve efficiency through integrated management of distribution centers and inspection rooms.
◆Repair of returned products and remanufacturing of existing products through repair, etc.
By inspecting the returned product and remanufacturing it by repairing the defective part, it is possible to improve the efficiency and cost reduction of the return work of the shipper (manufacturer) and perform quality control similar to the product.
◆Responding to BTO (Build To Order) and set work requested by customers
Assemble multiple parts, perform operation tests, and set work according to customer requests. Achieve product-like quality control and improved customer service to end users.