– Voice response system that confirms by voice in cooperation with 3PL service and eliminates input mistakes and acceptance mistakes –
The system standardizes the complicated work of sorting returned goods by voice response and screen display. In addition, voice confirmation of the input values enables accurate acceptance inspection results.
1. Features/Functions of Returned Goods Inspection System
Streamlines return inspection and sorting operations with voice confirmation and screen display.
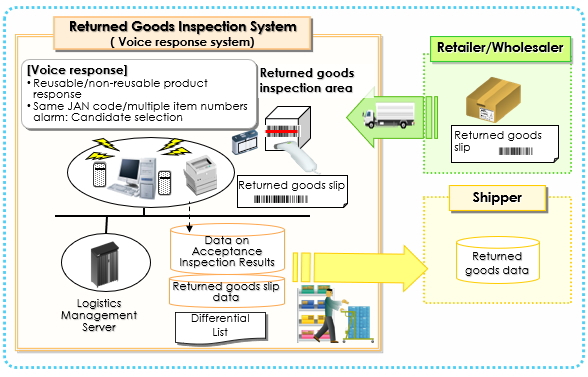
* Click the image to see the enlarged image. |
Improves the accuracy and work efficiency of inspection and sorting by checking (seeing) on the screen and checking (hearing) by voice. Multiple products or part numbers managed with the same JAN code can be selected from the screen list.
In addition, by interlocking the return and acceptance inspection results data with the inventory management system, it is possible to manage locations by product/product category and discarded items for each month of acceptance inspection (optional function). |
2. Problem and solution steps (example)
STEP 1: I want to do accurate and quick acceptance inspection.
■Issue |
- I want to sort products to be reused quickly and accurately by product (item).
- We want to complete the acceptance inspection of large lots of returned goods that are concentrated on the closing date in a short period of time.
|
⇒Solutions |
- By confirming the acceptance sorting criteria (reuse target products, disposal target products, etc.) and the input quantity by voice response, it is possible to perform reliable work by “seeing” and “listening”.
- Returned goods that have been processed for acceptance in one line can be divided into multiple acceptance lines/work locations for parallel acceptance processing by using the incoming No. management.
|
STEP2: I want to improve the efficiency of product management, which is prone to errors.
■Issue |
- There are cases where multiple part numbers/products are managed under the same JAN code, and it is easy to make mistakes in the way products are sorted, so we want to make it easy for anyone to inspect, sort, and manage them.
|
⇒Solutions |
- Multiple product numbers and products with the same JAN code can be master registered and managed in the acceptance inspection system, and at the time of acceptance inspection, they can be confirmed by voice response and selected from a list of candidates on the screen.
|
STEP3: I want to make advanced use of the system.
■Issue |
- I want to manage the return shipping costs.
- We want to manage the difference between the quantity on the “return slip” and the actual acceptance of the “returned goods,” as well as the difference in quantity between “loaned goods” and “returned goods.
|
⇒Solutions |
- The system allows you to register freight charges for returned goods in the unit of receiving No. and manage the data together with the results of returned goods.
- Differences can be extracted by matching the input contents of return slips and the results of acceptance inspection in the receiving No. management unit.
|