第150号acom Logistics Center HERLITZ(ヘルリッツ)ドイツ文具メーカー(2008年6月17日発行)
執筆者 | 鈴木 準 (サン物流開発 代表) |
---|
目次
- ●会社概要
- ●生販配一体、駅直結の物流センター
- ●荷下ろし・積み込みの自動化
- ●二つのサイズのパレットを併用
- ●バックアップを取ったコンベヤシステム
- ●ミニロード(AKL)自動倉庫
- ●自動補充+自走のピッキングシャトル
- ●ABC分析でピッキング方式選定
- ●DPSペーパーレスピッキング
- ●カートンの自動仕分けシステム
- ●パレットの自動積み込み
- ●WMS (Warehouse Management System)
●会社概要
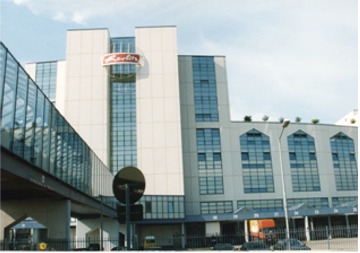
シティホテルのような物流センター
1904年、ドイツのベルリンに文房具と紙製品の卸売商としてCARL HERLITZ氏が創業した。これまでの100年間、優れた学校用文具を開発してきたHerlitz(ヘルリッツ)は現在15.000アイテムもの製品を取扱っている文具メーカーである。
ドイツでは子どもから老人まで、なんと”93%”が知っているという超有名人気ブランドである。ヘルリッツは、交通安全に役立つ歩行者用リフレクターの製造・販売も行っており、日本でもインターネットで買うことができる。ヘルリッツ社の売上の50%はドイツ以外のヨーロッパである。
我々の訪問した施設は製造工場と物流センターを併設したもので、日本では余り無いケースの物流センターである。しかし、生産地の移動により、ドイツでの生産は10年前よりは減少し、工場機能は減衰している。このセンターの建設には東ドイツの経済復興支援を目的に、政府から投資の10%の補助金が支給された。
このセンターへの入荷は隣接の工場と他地域の自社工場から50%、残りはアジアからの輸入である。ヘルリッツ社は業績好調のため1994年に新しい物流センターを建設した。このレポートは1999年と2006年の2回にわたる訪問のレポートである。
ここではパレット用の自動倉庫とカートンとコンテナの自動倉庫を持ち、ペーパーレスピッキング、ピッキングシステムへの自動補充及びトレーラーへの自動積み込み、2階建ての自動倉庫など優れた物流システムをもった先進的物流センターである。なお、acom Logistics Centerは物流子会社である。
●生販配一体、駅直結の物流センター
ヘルリッツ社の工場と物流センターはベルリンのテーゲル空港から10kmのブランデンブルグランド、ファルケンシー町にある。建物は7階建てで、一見したところ近代的なシティホテルのようである。建物の前の道路を隔てたところにDBドイツ国鉄の駅があり、顧客、従業員の駐車場がある。そこにヘルリッツ社の入口があり、階段を上がり、数十メートルの総ガラス張りのペデストリアンデッキを通ってタワーと呼ばれる建物の中央の総務部ビルに入る。大都市のシティホテルの様なビルは裏側に廻ると様相は一変する。
50台以上のトレーラーが接岸できるトラックのホームがあり、パレットと卜-トボックスの高層自動倉庫が目に入る。自動倉庫はタッカクレーン17台、奥行き100 mの規模である。それに加えてピッキング用にマニュアル運転のスタッカークレーン5台を持つ5,000 パレット収容の機械化倉庫もある。
日本の場合、地価の問題か工場と物流センターは離れた場所にあることが多く、工場・物流センター間は横持ちされている。欧米では生・販・配が一体化している例が多い。然し、最近は欧米も輸入が多くなったので、物流に変化がみられる。
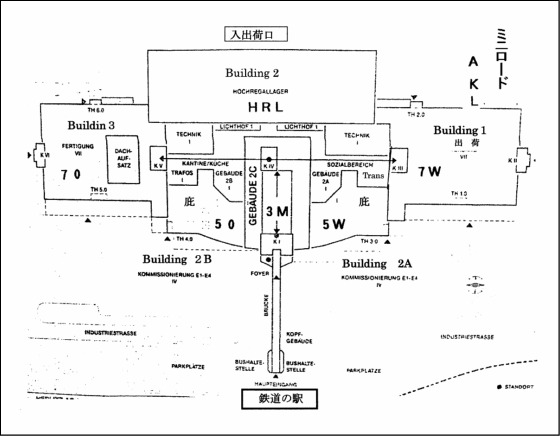
物流センターは、製造、保管、オーダーピッキングの総合ビルが接続した4棟の高層ビルからなる。建物は職員用の出入口を中心に南北を軸にした左右対称のデザインになっている。建物の平面図の70と7Wが東西に位置している。この7階建てのビルの間に5階建てのビル50と5Wがあり、3階建ての総務部用ビル(3M)が中央に位置している。
パレット用自動倉庫(HRL)は東西にある5階建てビルの裏側に有り、増築の余地を残している。西側の7階建てのビルの裏には自動倉庫ミニロードが南北に位置しているがこれも増築可能である。自動倉庫以外のビルの高さは37m、幅70m、建物全体の長さは335 m、総床面積は11万5,000㎡である。使用したコンクリートは15万立方メートル、鋼材はエッフェル塔の2倍の1万3千tである。
1階には59台のトラックが接岸できるドックレベラー付きのゲートが51あり、8つのゲートには自動積み込み装置がある。建物全体には16個の中電圧トランスを通じて1,000万ワットの電力が供給されている。出力250万ワットの2台の非常用発電装置もある。また、天然ガスによる7,500Kwのカロリーのあるボイラーを備えている。
●荷下ろし・積み込みの自動化
近くの工場で作られた製品はトレーラーで物流センターに運ばれてくる。パレットの積み下ろしはシャトルローダーで自動である。1,200×800のヨーロッパスタンダードのパレットが3列で一度に27枚載せられる。
パレットにはユニークバーコードが付けられていて、コンピュータで管理されている。
パレットは重量とサイズがチェックされ、積載商品の内容とパレットのバーコードが紐付けされ、パレット・ハンドリング・システムで目的の場所に運ばれる。パレット・ハンドリング・システムはローラーコンベヤ、リフトテーブル、ターンテーブル、チェーンコンベヤ、そして1.5tのインターフローリフトから構成されている。
継続的に入荷する定番商品はトラックから直接パレット・ハンドリング・システムに置き、アキュムレーション・コンベヤ・ラインに搬送する。コンベヤラインに平行して歩廊があり、検査やメンテナンス、荷物のラベリングがし易い様になっている。オーダー・プロセスの情報はコンピュータで管理されており、荷受けエリアにもリンクし交信している。荷受けエリアには自動荷下ろし用のドッキングステーションが2基あり、他にコンベヤによる荷下ろし用の電気制御の荷下ろしブリッジのついた10以上ものドッキングステーションがある。全体で1時間最高300パレットの荷下ろしが可能である。
カートンとコンテナ用のミニロード自動倉庫(AKL)に保管する荷物はパレタイズ貨物と同様の方法で荷受けされる。荷受けしたコンテナ又は段ボールカートンにはIDのバーコードラベルが貼られる。コンベヤラインによりミニロードに運ばれる。
●二つのサイズのパレットを併用
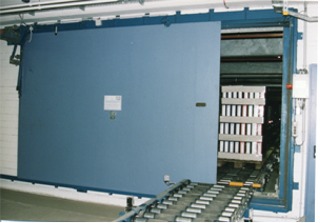
自動倉庫の自動開閉扉
自動倉庫はコンクリート建築で4万9、000パレットを収容する。パレットはユーロパレット(800×1200)と1,400×1400の特殊パレットを使っている。ラックには1tのユーロパレット3枚か1.5tの特別サイズのパレット2枚が保管出来るように設計されている。特別サイズのパレットはユーロサイズのパレットの底面の形状を共通にしているのでセンター内での搬送は問題ない。自動倉庫のサイズは奥行き140m、高さ40m、幅48mである。この自動倉庫は厚さ80cmの鉄筋コンクリートの基礎の上に建っている。
万一の火災発生時のために必要なだけの水が水槽に貯水されている。パレットの入出口には防火扉があり、パレットの通過時だけドアが開く。煙探知器は63個ついており、ドイツの防火基準クラスⅣに適合している。尚、冬季は庫内温度は5~8℃に保温される。高度の処理能力が要求されるために、自動倉庫内の一部を二階建てにしなければならなかった。他の自動倉庫とは防火壁で遮断されており、2台の高さ40mのスタッカークレーンが、もう一つの防火壁で遮断された区域の1階と2階の各8通路で作動している。
この方法によって達成できる取扱量には、例えば、スタッカークレーンにテレスコピック・フォークを2組取り付けたり、一つのレール上を2台のスタッカークレーンを走行させている。両サイドの自動倉庫のフロントエンドでインターフロアのコンベヤを使用することにより、各フロア一間を結ぶことが可能となった。
18台全てのスタッカークレーンは、積載可能重量1.5tである。水平走行速度毎分160mで、垂直走行は毎分60mである。パレットのピッキングや入庫時のフォークのサイクルタイムは約10秒である。1台のクレーンが毎時25ダブルサイクルで稼働すると最大毎時750パレットが入出庫出来る。自動倉庫は鉄骨構造のコンクリート建築で4万9,000パレットを収容できる。
パレットにはIDのユニークバーコードが付けられていて、コンピュータで管理されている。パレットは重量とサイズがチェックされ、積載商品の内容とパレットのIDコードが登録され、パレット・ハンドリング・システムで目的の場所に運ばれる。パレット・ハンドリング・システムはローラーコンベヤ、リフトテーブル、ターンテーブル、チェーンコンベヤ、そして1.5tのインターフローリフトから構成されている。
通常の荷受け商品にはパレタイズされていない物もあり、これはパレタイズする。又、積み付けの悪いパレットは積みなおし、パレットの悪いものはパレットを交換する。
継続的に入荷する定番商品はトラックから直接パレット・ハンドリング・システムに置き、アキュムレーション・コンベヤ・ラインに搬送する。コンペヤラインに平行して歩廊があり、検査やメンテナンス、ラベリングがし易い様になっている。オーダー・プロセスの情報はコンピュータで管理されており、荷受けエリアにもリンクし交信している。
荷受けエリアには自動荷下ろし用のドッキングステーションが2基あり、他にコンベヤによる荷下ろし用の電気制御の荷下ろしブリッヂのついた10以上ものドッキングステーションがある。全体で1時間最高300パレットの荷下ろしが可能である。
カートンとコンテナ用のミニロード自動倉庫(AKL)に保管する荷物はパレタイズ貨物と同様の方法で荷受けされる。荷受けしたコンテナ又は段ボールカートンにはIDのバーコードラベルが貼られる。コンベヤラインによりミニロードに運ばれる。
●バックアップを取ったコンベヤシステム
マテリアル・ハンドリング・システムと自動倉庫を結ぶ通常のコンベヤシステムとは異なり建物の東西の末端まで150mを結ぶ効率の良いコンベヤシステムが設置されている。
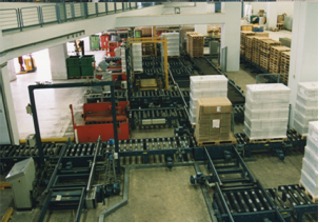
一か所のトラブルでは止まらない
パレットの移動が大量であるために、スタッカークレーンによる入出庫作業は自動倉庫の両端の二つのフロアで行っている。幾つものバッフアーポジションのあるチェーンコンベヤが各通路に繋がっている。ローラー・リフト・テーブルによりチェーンコンベヤは入庫されたり、出庫されたパレットが搬送されるローラー・コンベヤ・ラインに繋がっている。
2番目のローラー・コンベヤ・ラインは平行して設置されており、ある一定の距離のもとで接続するリフティング・テーブルやチェーンコンベヤによりサーキットを作り出すことが可能である。バッフアー機能に加えて、この機能があるので、コンベヤが故障した場合には、荷物を載せたパレットのルートを変更することができる。このサーキットは幾つかのサーキットをリンクすることで六つのインター・フロア・コンベヤと結びついており、7階建てビルと5階建てビルの間を結んでいる。所謂コンベヤタワーは相対的に設備の設置が左右対称になっているので自動倉庫の両端と同じデザインになっている。
●ミニロード(AKL)自動倉庫
段ボールカートンやトートボックス用のミニロードは600mm×400mm×250mmのコンテナとそれより小さい300mm×200mm×50mmまでのダンボール箱を扱う。ミニロードは2階建てになっていて、1フロア2台、計4台のスタッカークレーンが二つのフロアに設置されている。ミニロードのサイズは奥行き82m、高さ28m、幅13.5m、72、000の保管ロケーションがある。
スタッカークレーンは水平走行速度毎分140m、垂直走行速度毎分50mである。テレスコピック装置がラックのユニットロード(コンテナ等の荷物)の両側に伸びている。90度回転するグリッパーの爪がユニットロードを覆うようにして掴むので、ユニットロードをスタッカークレーンのリフティング用の台車に引き寄せることができる。
また、ユニットロードをラックの保管場所に簡単に押し込むことができる。1サイクル10秒である。スタッカークレーンにはコンベヤの入出庫装置があり、ラックから1個づつ取り出し、コンベヤに3個のユニットロード(カートン)を載せ入出庫する。1台のスタッカークレーンで毎時77個の取り扱いができ、全体で1時間600個の入出庫ができる。
ミニロードはビル7階(7W)すべてに商品を供給することができる。商品は1階の荷受エリアから自動倉庫に格納される。商品は2階と4階から高速自動仕分機とオーダーピッキングエリアへ供給される。製造現場には未完製品と半製品が供給され、完成品は5階と7階に保管されている。カートンボックスおよびトート(コンテナ)の搬送を行うコンベヤシステムはロ-ラーコンベヤとベルトコンベヤである。ユニットロードをスタッカークレーンヘの搬送と同時に行われるミニロードからの搬出は二つの階で行われている。各階は2基のパテノスター型エレベーターで繋がっており、各パテノスター型エレベーターの能力は毎時750個である。
●自動補充+自走のピッキングシャトル
グリーティングカードのピッキングシステムは天井のレールにガイドされ、そのレールから電力の供給を受けるコンピュータ搭載の電動台車(ピッキングシャトル)で、フローラックから台車上のDPS(デジタルピッキングシステム)を備えた19の集品箱にフローラックから一括ピッキングした商品をカートに載せた客別のコンテナの表示の数量をスロットに種まきする方式である。グリーティングカード以外の小物のピッキングにも利用している。ピッキングする商品を保管するフローラックには5、000アイテムの商品を置くことができる。又、人の手の届かないフローラックの上部には2,700アイテムの商品を置くリザーブラックがある。
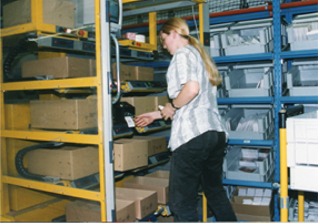
自走のピッキングシャトル
フローラックのピッキング用ラックには2箱が置けるダブルビン方式である。また、補充はミニロードからリザーブまたはピッキングラックに自動的に補充している。商品はコンテナに入れてフローラックに収納されており、ピッキングして商品が無くなるとコンテナのバーコードをハンディスキャナーでスキャンし、無線でコンピュータに伝送することにより、コンピュータが補充指示を出す。日本ではこのタイプのピッキングシステムは見られない。
自動制御のピッキングシャトルにはコンピュータとラベルプリンター、モニター、無線装置が搭載されており、サーバーと無線で情報交換を行い、コンピュータの指示により指定の順路で移動する。走行速度は毎分60mである。ピッキングシャトルの上部にはモニターがあり、ピッカーにピッキングの指示をする。ピッキングシャトル上の19のオーダーの箱を置く棚にはデジタルディスプレイと投人を指示するランプがある。
ピッキングシャトルはIDポイント(スタート)に行き、最初にコンピュータの指示したサイズの出荷箱を取り指定の棚に配置する。プリンターから1バッチのピッキング・リストがプリントアウトされる。スタート準備が完了し、運行を指示すると、ピッキングシャトルは最初にピッキングするフローラックの前で停止する。以後作業はコンピュータの指示により、自動的に走行し、ピッキング位置では自動的に停止する。この制御はフローラックの前面に貼られたバーコードをスキャンすることで行われる。
ピッキング情報はモニターに表示される。ピッキングすべき商品の棚の段がピッキングシャトルの両側にランプや表示する。そして、各オーダーの出荷箱の棚にはピッキングする数量が表示される。ピッカーは商品を指定の数だけ取って箱に入れ、オーダー毎のピッキング完了ボタンを押し、商品のEANコードをハンディスキャナーでスキャンする。プリンターからラベルが発行される。このラベルを商品に添付して出荷箱に入れる。これを繰り返し、ピッキングが終了すると、情報はコンピュータにフィードバックされる。出荷箱は出荷ラインに送られ、検品後、梱包し、出荷用自動仕分機に送られる。1人時のピッキング量は500個から750個である。
●ABC分析でピッキング方式選定
オーダーピッキングの方式は出荷量のABC分類により決まる。ヘルリッツ社ではABCD4グループに分けて最適なピッキング方式を採用している。
Aグループには150アイテムを選び、パレットラックに保管しピッキングする。補充はパレット自動倉庫(HRL)から補充する。ピッキングはカートを利用した単純なDPS方式で詳細はDPSペーパーレスピッキングの項を参照して下さい。
BとCアイテムには2、500アイテムを選び、グリーティングカードと同じピッキングシャトルを使い、商品はフローラックに保管し、人の手の届かないフローラックの上をリザーブとし、補充はミニロードからコンテナ搬送システムを通じ、ミニロードのスタッカークレーンと同じ機構で商品をフローラックに自動補充している。
Dアイテムは1、500アイテムで平棚に保管し、補充もマニュアルである。
●DPSペーパーレスピッキング
DPS (Digital Picking System)はアメリカではPick to Light と呼ばれている。点滅するライトとデジタルディスプレイのガイドによりピッカーがピッキングするからである。DPSはヨーロッパで生まれ、アメリカのラピスタン社から日本のトーヨーカネツが日本に持ち込み、生協を中心に普及成長し、今ではオーダーピッキングの定番になっている。
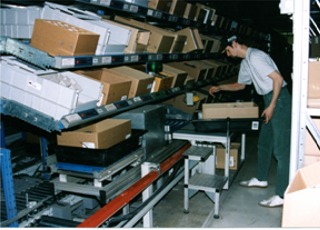
DPS
オーダーの商品の容量計算により、出荷箱がコンピュータにより指定される。次にユニークバーコードのついたトレイを取り、出荷箱に荷札を貼ってトレイに載せる。
トレイのバーコードをスキャンして搬送コンベヤに送り出す。ピッキングする商品はフローラックに置かれている。フローラックの下に出荷箱を載せたトレイの搬送コンベヤがある。
フローラックは適当なアイテム数で区分して一人のピッカーが担当するゾーンとする。ゾーン単位にピッキングステーションがあり、コンベヤで搬送されて来たトレイは搬送コンベヤから水平にピッカー側に押し出され、ピッカーが作業し易い高さにリフトアップされる。
これと連動して、ピッキングするアイテムのスロットに付けられたデジタルディスプレイと通報ランプが点灯し、ディスプレイにピッキング数量を表示する。ピッカーはランプの点滅する場所に行き、ディスプレイが表示する数量を取り、ピッキング完了ボタンを押す。
もし、欠品等で修正が必要な場合はステーションにあるキーボートとハンディスキャナーで修正し、情報をホストコンピュータに送る。未完のコンテナは次のピッキングのあるゾーンに自動的に運ばれる。
尚、商品配置は出荷頻度の高い商品をピッキングステーション側に置くことにより歩行を減らしている。1ゾーンの点灯したランプを全部消し、ピッキングが完了するとトレイを搬送コンベヤに押し出す。ピッキングの完了したトレイはトレイから自動的に出荷箱を下ろし、重量で検査し、合格したカートンは梱包して方面別仕分けの自動仕分機に送られる。DPSのピッキングラインは3ラインあり、1ラインには8人が配置されている。
●カートンの自動仕分けシステム
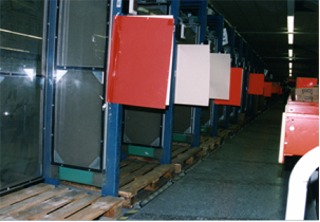
パレタイズした貨物は出荷場へ自動搬出
出荷用のコンテナやカートンを仕分ける自動仕分機はデンマーク、グリスプラント社製のチルトトレイソーターである。全長150mのループ式で、駆動は4台のリニアモーターを使用していので騒音は低い。仕分け方面数は80シュート、仕分け能力は毎時7千から8千個である。仕分けはカートンに貼られた荷札のバーコードをレーザースキャナーでスキャンすることにより行われる。
シュートが満杯になると満杯検知器が働き、トレイに乗っている満杯のシュートに行く荷物は満杯が解除されるまで仕分けられず、トレイに乗ったまま回遊する。シュートはローラーとベルトコンベヤで作られており、シュートに仕分けられた荷物にブレーキを掛け、荷傷みを防止する。
バーコードの読み取り不良はミスシュートに落とされ、修正後再投入される。シュートに仕分られた荷物は二つの方法でパレタイズされる。一つは大口顧客用で自動仕分機のループの内側シュートに設置された積み付け装置である。シャワールームの様に三方に壁を付けたコの字型の積み込み枠の中に置かれたパレットに荷物を積む方式である。
シュートから取った荷物の荷札のバーコードを読み取り、枠の中のパレットに荷物を積み付ける。この積み付けは情報システムにより管理されており、満杯になるか、又は1オーダーが終了すると、その情報を端末からインプットすると、積み付けた荷物の明細書がプリントアウトされる。
この積み付け装置の後ろには自動倉庫のスタッカークレーンと同じ様な機械があり、積み付けの終わった枠の後ろから荷物を取りに来る。自動的に枠のスタッカークレーン側の壁(扉)が外され、対向する二方の壁が広がる。荷物はスタッカークレーンにより引き取られ、空のパレットが供給される。積み込み装置には0、1、2、3のキーボードと上下左右に向いた矢印のキーボードがあり、簡単に情報伝達ができる用にしている。パレットに積まれた荷物はパレットコンベヤに移され、荷崩れ防止のストレッチフィルムを巻き、出荷場に運ばれる。ここには10名の従業員が勤務している。
自動仕分機のループの外側のシュートはマニュアルで売上の少ない顧客向けであり、ここでは5人が勤務している。
●パレットの自動積み込み
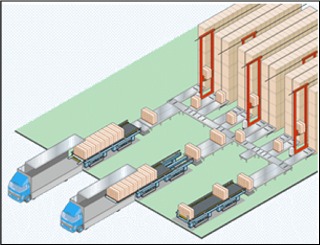
自動積み込みのシャトルローダー
出荷エリアには様々な形のパレットが運ばれて来る。同じ形状の荷物のフルパレット、同じ荷物だが端数のパーシャルパレット、自動仕分機で仕分けた様々な形の荷物を積んだパレット、荷崩れ防止のフィルムの巻いていないパレット等である。ここでは、顧客が指定するパレットに積み替えることもある。トラック輸送に向いていないパレットの荷姿を修正する。1台のトラックに積み込む最大18枚のパレットがアキュムレーションコンペヤに累積される。
満杯又は端数でも積み込む荷物はマテリアルフローの情報システムにより積み込み指示が出される。2台あるトラックヘの自動積み込み装置(ローダー)の1台がパレットを引取に来て3列6行にパレットをローダー上に並べる。トラックローダーは数分でトラックヘの積み込みを完了する。勿論、通常のフォークリフトによる積み込みも併用して行っている。
●WMS (Warehouse Management System)
物流センターの統合管理システムは多数の独立したサブシステムに分割されている。これらのサブシステムは、荷受けと出荷とパレット・ハンドリング・システム、パレット自動倉庫、ミニロード、オーダーピッキングシステムと自動仕分けシステムである。
統合管理システムはHierarchy (ピラミッド)構成になっており、多段階のレベルに分割さている。最底辺のレベルはレベル1であり、モーターの回転等である。レベル2は論理的オペレーションで、プログラミングが可能な論理的コントロールがこのレベルである。
レベル3はマテリアル・フロー・コンピュータで、物の流れと各サブシステムのデーターをモニターしている。これによりシークェンスコントロールが正しく行われているかを確認する。サービスルームには、グラフィックモニターがあり、全ての搬送作業のトラッキングをしており、マテリアルフローに連結しているデーターを呼び出している。ミスやトラブルが発生した場合にはその発生場所や種類が明確にモニターできる。
システムマネージメントコンピュータは上位から二番目の高い位置にあり、起源、行き先の原理に基づくサブシステムをコントロールしており、統合されたシステム全般に渡って物の流れを把握している。このシステム・マネージメント・レベルでは下記のプロセスをモニターし、管理している。
最近は産地がアジアに移行しているために、ここでの製造は減少し、ボールペンの包装など流通加工が多くなっている。また、繁忙期は新学期であり、年間の物量の変動が激しいので無駄なスペースが多くなっているので3PL、外部企業の物流業務受託も進めている。なお、この施設のエンジニアリングはドイツのマテハンメーカー”マンネスマン”である。マテハン機器はクリスプラント、デマッグなどである。
以上
(C)2008 Jun Suzuki & Sakata Warehouse, Inc.