第220号保管費を削減する手順(2011年5月24日発行)
執筆者 | 平野 太三 (有限会社SANTA物流コンサルティング 代表取締役社長) -物流改革コンサルタント Dr.SANTA- |
---|
執筆者略歴 ▼
目次
1.保管費削減のポイント
売上高の拡大が難しい時代では、取り扱いアイテム数の増加と、在庫金額の増加が企業の優先課題のひとつになっている。在庫が多くなると在庫スペースが不足し、作業エリアも縮小されることになるので作業効率も悪化する。それでも在庫スペースが不足すれば、外部倉庫を使わざるを得なくなり、外部保管費・横持ち輸送費・入出荷作業費・棚卸作業費、在庫管理作業費のいずれもが増加してしまう。
この状況下において、保管費を削減するポイントとしては、「①在庫の削減」「②保管効率の向上」「③保管費の安い倉庫の活用」が考えられる。今回はこの改善手法をわかりやすく解説したい。
2.在庫金額の削減
在庫削減ができれば企業によってのメリットが大きいが、いざ在庫削減に取り組もうとすると「総論賛成、各論反対」になってしまう。「在庫削減を行うと欠品が増加してしまう」という思い込みが一番大きい。すべてのアイテムを一律に20%在庫数を削減するのであれば欠品は勿論増加する。誤解が無い様に言うが、少ない在庫を増加させ、多い在庫を少なくすることが在庫管理である。よって、うまく機能すれば、「在庫金額は減少するが、欠品アイテムも減少する」ことができる。
これを実現させるためには、「在庫の分析」「物流コストの可視化」「発注方法の見直し」が必須である。物流コストを可視化する方法として、在庫保有日数(今の出荷ペースで何日分の在庫があるか)が1年以上あり、在庫スペースを多く取っている過剰在庫のアイテムをいくつか抽出することから始める。うまくいっていない商品は、どの程度物流コストが増加しているかを可視化することが目的である。
図1を見て頂きたい。
図1 発注ロットと保管費の関係
*画像をClickすると拡大画像が見られます。
結果として、6カ月で在庫が無くなる例であるが、毎月入荷することができれば、保管費の削減は大幅に削減できる。しかし、毎月入荷が発生する場合は、仕入単価の増加、及び、入荷関連費用が増加する。それぞれのメリット、デメリットをすべて数値化し、その結果で会社としての発注基準を作れば良い。
「交渉に交渉を重ねても最小ロットで半年分の在庫を超えてしまう商品は廃番にする」とか、「戦略的に品揃えが必要な商品は営業利益が減少しても最小ロットで発注する」が基準作りの例である。この様な方法で皆様の会社でも在庫の基準を持って欲しい。在庫を何カ月分多く持てば、どの程度の物流コストが増加し、仕入単価増加の何%に該当するかを把握する。
つまり、「営業利益重視、生産効率重視の考え方」から「経常利益重視の考え方」にシフトして仕入量を調整すれば、これ以外にも色々な案が出てくるものである。私はマーケティング理論は皆様にお話をするほどの知識は持っていないが、見せ球商品(品揃えが多い売場ほど消費者の立ち寄り回数が多い)の理論は一考の余地はあると思う。アイテム数を増加される方が最終的な売上が増加するのか、アイテム数を少なく絞って低単価の商品を提供する方が最終的な売上が増加するのか、を比較するのである。
物流コストから考えると、後者の理論の方が物流コストが大幅に削減することは述べておく。ここでは問題提起とさせて頂きたい。
3.保管効率の向上
在庫削減が実現できない場合でも保管費を削減できる方法がある。物流センターの在庫商品を出荷動向で分別をすると、「保管効率を優先する在庫」と、「作業効率を優先する在庫」「保管効率と作業効率の調整が必要な在庫」が存在する。「保管効率を優先する在庫」の例としては、「過剰分在庫」「シーズン外在庫」がある。
図2の様に、棚保管よりもケース保管、ケース保管よりもパレット保管の方がスペース効率は良い。言うまでも無いが、パレット積みの場合でも奥行きのパレット数が多いほどフォークリフトの通路幅の比率が少なくなるため、保管効率が変わる。
図2 保管効率の向上
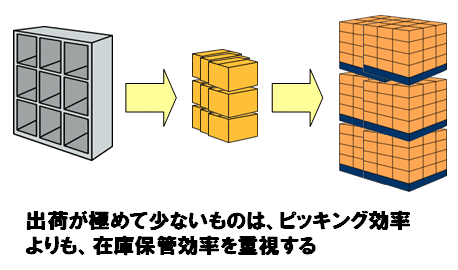
在庫分析( ロジスティクス・レビュー第176号「在庫削減で無駄な物流コストを大幅に削減」で詳しく述べているので参考にして欲しい)をすると、在庫保有日数が半年以上の在庫を持つアイテムが必ずある。この半年分を超えた在庫部分は論理的には半年間出荷が無い商品であるため、作業効率よりも保管効率を優先する在庫配置を取れば良い。(但し、過剰分在庫が少ない場合、極論で言うと1ケースの場合は在庫分割する必要は無い)。
また、シーズン外在庫であれば、一部ピッキングエリアの在庫確保の分を除き、これも保管効率優先の在庫配置を取ればよい。半年超過分の在庫配置見直しは現実的にはイレギュラー処理があるため3カ月毎には必要であるが、処分対象品を除けば保管効率を継続して行う確率が高いため、大幅な在庫配置の見直しは必要ない。
「作業効率を優先する在庫」は、毎日大量に出荷する商品と、大量出荷は無いがバラ出荷が多く出荷頻度が高い商品、ケース出荷が多い商品がある。よく出る商品は、出荷作業時間(ピッキング時間と補充時間の最適化)が優先になる。
「保管効率と作業効率の調整が必要な在庫」は、2~3カ月に1回しか出荷が無い商品であっても、100アイテムあれば平均すると毎日出荷が発生するため、倉庫のレイアウトに対応してシミュレーションする。例えば、在庫保有日数を1週間持った場合は、何坪必要かを計算し、作業効率と保管効率のバランスの良い倉庫レイアウトを構築する。この方法は、在庫容積分析が必要になるためかなり高度な物流管理レベルが必要であるが、是非トライして欲しい。
また、お金がかかる改善であるが、棚の上のスペースに中2Fを作る方法も考えられる。例えば中2Fを構築することに1000万円かかっても、外部委託保管スペースが100坪程度削減できるのであれば、「外部保管費坪単価4000円×100坪×12カ月=480万円/年。注意:坪単価は場所により違う」となるため、ほぼ2年でペイできることになる。
4.保管費の安い倉庫の活用
在庫を削減し保管効率を向上させても、まだ倉庫に入りきらない場合は、外部倉庫を借りる必要がある。ただ、前述した分析手法で長期間動かさない商品であれば交通に不便な場所の安い倉庫を借りても良い。日本国内であっても、通常の保管費の1/3以下の料金で借りることが可能であるため、外部支払保管費を大幅に削減することができる。
ただ、安いからと言っても多少は荷動きがある商品を持って行ってしまうと、横持ち輸送費や入出荷人件費がかさむためお薦めしない。これも「保管費の月間削減額と入出荷作業料月間増加額+横持ち運賃月間増加額」をシミュレーションしておく必要がある。決算処分待ち商品、超過剰在庫であれば、この運用で問題は無い。
また、議論として坪単価が安い倉庫を最初から借りていれば良いと思う方もおられるかもしれないが、その方法はあまりうまくいかない。辺境地であれば坪単価が安いが、集荷してもらえる運送会社が限定されており、競合が少ないと運賃単価が今よりも高くなる可能性がある。
仮に、運賃単価に問題が無い場合でも、運送会社の立地条件の関係で集荷時間が早くなってしまうことも多い。その影響として、お客様への受注締め時間が繰り上がってしまい、顧客サービスが落ちることにつながるかもしれない。他に社員の通勤の問題や、人口が少ない地域ではパートの雇用の問題も発生する。よって、これらのことをひとつひとつつぶしていかなければ、倉庫料が安くなっても全体のコストが増加してしまえば意味が無いのである。
5.保管費の管理方法
物流管理の基本行為として、効果検証がある。物流改革は改善実行をしても残念ながら効果が出無い場合がある。その理由が、「対策に漏れがあったのか」「対策に無理があったのか」「対策を実行していなかったのか」により、今後も継続していってよいのかを判断が変わる。
図3をご覧頂きたい。
図3 在庫金額、在庫量の確認
*画像をClickすると拡大画像が見られます。
この様な管理指標があれば、保管費、在庫金額、保管効率の状況チェックができ、早く対策をたてることが可能である。在庫金額の管理も勿論必要であるが、在庫のスペース効率を検証するためには、在庫容積を算出しなければならない。基本的には箱サイズを計測して、1ケース当りの物流容積を算出することが望ましいが、在庫アイテム数が多い企業にとっては不可能に近い。
その場合は、パレット積みの在庫ケース数を商品毎に登録し、容積を計算する方法をお勧めする。厳密に言うと商品毎にパレット積みの高さが違うが、近似値がわかるだけでも充分に物流管理のレベルがあがる。
以上
(C)2011 Taizo Hirano & Sakata Warehouse, Inc.